In the following, we would like to give a brief overview of the essence of hydrophobisation in construction chemistry or for construction chemical applications.
Hydrophobisation - what is it?
The hydrophobisation of building materials means to make them water-repellent or to equip them with water-repellent properties. The hydrophobic agent occupies the pore and capillary surfaces and makes them water-repellent. Capillaries and pores are not completely sealed, however, so that the breathability (diffusibility) of the respective material is preserved and remains intact.
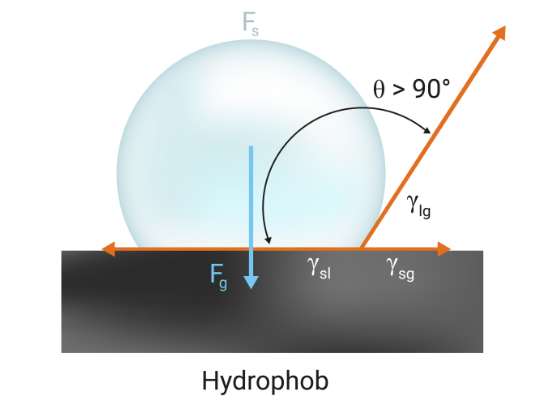
Fig: If the angle is > 90°, the surface is water-repellent, i.e. hydrophobic.
Hydrophobing agents based on organic silicon compounds always require moisture to react to the final active ingredient (silicone resin), but this is available in sufficient quantities in every building material or substrate.
In order for the effectiveness to unfold optimally, it must be ensured that the silicone resin molecules are firmly bound to the surface of the material and that there is also a corresponding depth of penetration into the substrate.
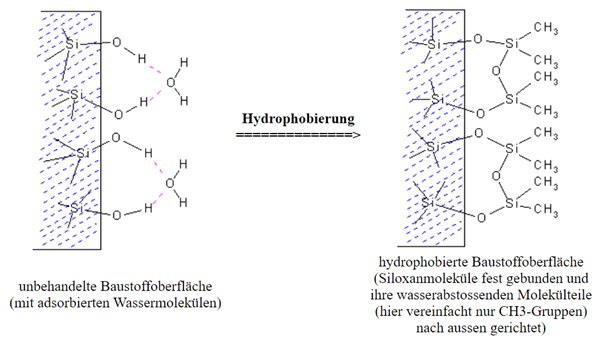
Source: Andrea Glatthor -
Baustoffchemie.de
Overview of the different active substances (org. Si compounds)
1. Alkoxysilanes (simplified often called "silanes")
In building protection, silanes are understood to be the alkylalkoxysilanes, while "anhydrolised silanes" in turn tend to belong to the alkylalkoxysiloxanes. Variants:
- dissolved in water-free alcohols (e.g. isopropanol)
- dissolved in aliphatic solvents
- emulsified in water (e.g. the triethoxyoctylsilane)
2. Alkoxysiloxanes (often simply called "siloxanes")
There are oligomeric and polymeric siloxanes, i.e. products with small and large molecules. Variants:
- Dissolved in aliphatic solvents.
- Emulsified in water.
- As microemulsion concentrate (silanes and oligomeric alkoxysiloxanes in a mixture). Silicone microemulsion concentrates (SMK) are a 100% silicone product that can be diluted with water to spontaneously form a microemulsion.
3. Silicone resins (alkyl polysiloxanes)
4. Alkali silicones
These are highly alkaline solutions of potassium siliconate. When applied to building materials, they react with the carbon dioxide in the air to form silanol as an intermediate stage, which then reacts to form the silicone resin. In the process, potassium carbonate (potash, K2CO3) is formed as a by-product, which can then make itself noticeable as a white coating on the surface and would be particularly disruptive on façades.
The products are mainly used for the factory impregnation of bricks, aerated concrete and similar building materials, but are also often contained in injection agents for subsequent horizontal barriers (there mostly in combination with water glass). These products are only recommended for the subsequent impregnation of gypsum building materials (e.g. if "white" gypsum plasterboards have been installed by mistake instead of the pre-impregnated "green" ones or if only partial areas are to be hydrophobised).
All four active substances ultimately result in a silicone resin as a reaction product on the surface of the building material:
Reaction with moisture
Silane -----------------------------------> Silicone resin
Molecule enlargement
Reaction with moisture
Siloxane -----------------------------------> Silicone resin
Molecule enlargement
Evaporation of the solvent
Silicone resin -----------------------------------> Silicone resin
Reaction with CO2 of the air
Silikonates -----------------------------------> Silicone resin
Molecule enlargement
Regardless of which type of water repellent is used, the end product of all of them is a silicone resin - but the molecular size of this silicone resin can be very different, depending on which of the above-mentioned starting materials is used. This is only of minor importance here, but should not go unmentioned. The entire presentation here has been greatly simplified.
5 Auxiliary materials
Additives include solvents such as isoparaffins, various benzines and special benzines as well as alcohols. Furthermore, various additives such as wetting agents, preservatives, emulsifiers and catalysts.
Overview of the most important types of preparation
1. Impregnating emulsions, water-based
Solvent-free, water-based emulsions made from combinations of silanes and/or siloxanes. There are also water- and solvent-free concentrates on the market that are first diluted with water and emulsified in the process before application (so-called microemulsions).
2. Impregnating paste
Highly viscous, i.e. thixotropic emulsions of siloxanes and silanes in water. Due to its high viscosity, the cream can be applied by roller, brush or airless spray without running off.
3. Impregnating solutions, solvent-based
Highly alkylated alkoxysiloxanes that cannot be dissolved or emulsified in alcohols or water. They only dissolve in petrol or similar organic solvents and have been state of the art since about 1970.
4. Impregnating solutions, aqueous
If the sales product is an aqueous solution, it is in most cases potassium methylsiliconates or potassium propylsiliconates. These have a rather limited range of application. They were the first organosilicon compounds on the market (approx. 1955).
Basically, there is the possibility to use the respective hydrophobing agents either:
In aqueous solution or emulsified in water or
Formulated in solvents (water-dilutable or also solvent-dilutable). The differences are due to the effectiveness of the various products and preparations as well as the depth of penetration, reaction, type of substrate, ezc and must be tested thoroughly before hydrophobising.
The correct application of various hydrophobing agents
When applying various waterproofing agents, the aim must be to achieve optimum effectiveness with as few unwanted side effects as possible. In principle, the better the penetration depth, the better the effectiveness of a water repellent. However, the optimum penetration depth for normal façades is only 2 to 4 mm, whereas for surfaces exposed to frost and de-icing salt (horizontal surfaces made of concrete, screed or paving stones), the optimum penetration depth is significantly higher (6-8 mm).
The penetration depth depends on various factors:
- The absorbency of the building material to be impregnated and its moisture content at the time of impregnation (as well as its chemical structure, since the chemical-physical interactions between the building material and the active ingredient solution are of decisive importance).
- the type of active ingredient (e.g. the size of the molecules, but also the chemical structure, because of the interactions just mentioned)
- the concentration of the active ingredient (a usual active ingredient content is 5%; too much active ingredient tends to do harm)
- the type of solvent (the optimal solvent changes depending on the active ingredient and the substrate conditions)
- the application technique (application method, application quantity, contact time, number of individual operations and time intervals between them).
Product groups/substance classes
Conclusion: Protection and extension of service life
The hydrophobisation of building materials and construction materials not only protects the material itself, but also improves thermal insulation, resulting in energy cost savings.
Donauchems product portfolio includes a range of hydrophobing agents.
Portfolio Additives
Portfolio Paint & Construction
For further information or quotations,
please contact us.
www.donauchem.at
Related links/sources:
Baustoffchemie.de
Dichtstoffhandel.de