Schaum ist bei Bier, Rasier- und Löschschaum durchaus willkommen. In vielen industriellen Anwendungen sind große Schaummengen aber ein störendes Nebenprodukt und müssen entfernt werden. Entsprechend breit werden Entschäumer in der Industrie eingesetzt. Wir geben einen Überblick über Schaum, dessen Stabilität, Charakterisierung und Auswirkung auf verschiedene Industrien sowie die Wirkungsweise und Arten von Entschäumern.
Was ist Schaum und wie baut er sich auf?
Flüssiger Schaum besteht aus kleinen Gasbläschen (in der Regel Luft), die durch flüssige Wände (Lamellen) voneinander getrennt sind. Direkt nach ihrer Entstehung steigen die Gasblasen in der flüssigen Phase nach oben an die Oberfläche. Damit stabiler Schaum entstehen kann, müssen grenzflächenaktive Substanzen (Tenside) in der flüssigen Phase vorhanden sein. Reine Flüssigkeiten (ohne grenzflächenaktive Substanzen) schäumen nicht, da die Schaumblasen platzen, wenn sie die Flüssigkeitsoberfläche erreichen.
Schaumstabilisierende Effekte durch Tenside
Ganz allgemein sind Tenside dadurch charakterisiert, dass sie hydrophile (wasserliebende) und hydrophobe (wasserabstoßende) beziehungsweise lipophile (fettliebende) chemische Gruppierungen im Molekül enthalten. Aufgrund dieser Struktur sind die Moleküle oberflächenaktiv, d.h. sie ordnen sich in der Grenzfläche flüssig/gasförmig derart an, dass der hydrophobe Teil nicht mit Wasser in Berührung kommt. Die damit verbundene Reduktion der Grenzflächenspannung schafft die Voraussetzungen für einen stabilen Schaum.
Das Anordnung der Tenside kann im Wesentlichen auf drei Arten erfolgen:
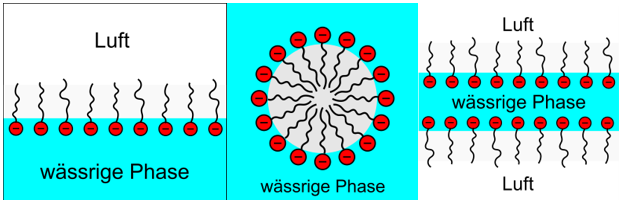
Quelle:
Wikipedia
- Die Tenside lagern sich an der Grenzfläche zwischen Wasser und Luft an und reduzieren so die Oberflächenspannung des Wassers (Abb. links).
- Die Tenside können sich auch in Wasser „lösen“, indem sie sich zusammenballen und sogenannte Mizellen bilden (Abb. mitte).
- Wenn die Flüssigkeit einen dünnen Film bildet, dann lagern sich die Tenside in zwei Oberflächenschichten an, wobei die hydrophilen Enden in die Lösung hineinragen (Abb. rechts).
Flüssiger Schaum entsteht somit immer dann, wenn sich die Oberflächenspannung des Wassers durch Anlagerung von Tensiden verringert und durch Aufschlagen, Einblasen oder ähnliche Methoden Luft eingebracht wird. Die so entstandenen Bläschen werden dann durch die Ausbildung einer Oberflächenschicht stabilisiert.
Kugelschaum – Polyederschaum – Zweidimensionaler Schaum
Schäume sind, thermodynamisch gesehen, instabile Mehrphasensysteme, weil sich ihre Formation ständig verändert. Betrachtet man den Lebenszyklus eines Schaumes, so stellt man fest, dass er im Laufe der Zeit Flüssigkeit verliert und dadurch seine Struktur ändert.
Dementsprechend werden zwei Schaumtypen unterschieden: Kugelschaum und Polyederschaum.
1. Kugelschaum
Kurz nach seiner Entstehung enthält der Schaum noch relativ viel Flüssigkeit. Die einzelnen Gasblasen sind kugelförmig mit einer dicken Lamellenschicht und deformieren sich gegenseitig noch nicht. Man nennt einen solchen Schaum daher auch „nassen Schaum“ oder „Kugelschaum“.
Für die Bildung von Kugelschaum ist die Anwesenheit von grenzflächenaktiven Stoffen nicht unbedingt notwendig. In diesem Fall sind die Stabilität und Lebensdauer des Schaumes von der Viskosität und die Dichte der Flüssigkeit abhängig. In niederviskosen Flüssigkeiten wie Wasser zerfällt der Schaum innerhalb von Sekunden. Schüttelt man z.B. eine Flasche Wasser, bilden sich aufsteigende Blasen, die beim Durchdringen der Flüssigkeitsoberfläche zerplatzen.
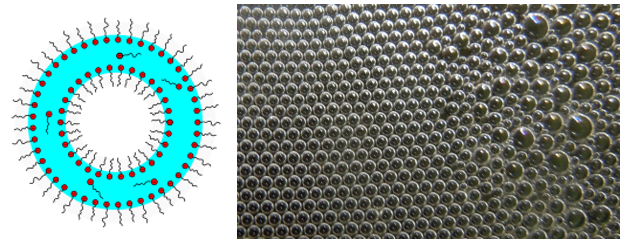
©
Kempf EK,
Order and Chaos,
CC BY 4.0 (Abb.rechts)
2. Polyederschaum
Bei einer Stabilisierung des Kugelschaumes an der Flüssigkeitsoberfläche, fließt aufgrund der Schwerkraft die Flüssigkeit aus den Lamellen nach unten ab (Drainage-Effekt). Die Lamellen werden dünner, die Gasblasen rücken näher zusammen, deformieren sich gegenseitig und werden zu Polyedern. Dieser Schaum wird als „trockener“ oder „Polyederschaum“ bezeichnet.
Sobald die Lamellen im oberen Bereich zu dünn werden, zerreißen die Schaumblasen. Verschiedene Gegenkräfte können allerdings den Drainagevorgang bremsen und den Lamellenbruch verhindern. Ursachen dafür sind die elektrostatische Abstoßung der Tensid Moleküle, der Marangoni-Effekt, aber auch äußere Einflüsse wie Temperatur und Viskosität.
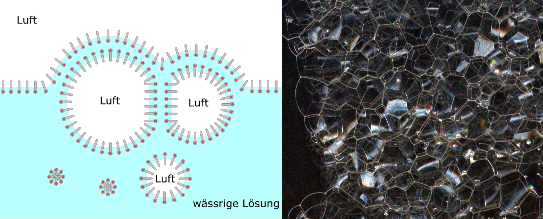
©
Roland.chem,
Schaumbildung,
CC BY-SA 3.0/
André Karwath, Foam - big,
CC BY-SA 2.5
Liegen bei Polyderschäumen die Polyeder nur nebeneinander, dann bezeichnet man diese Polyederschäume als “Zweidimensionalen Schaum”. Diese Art von Schaum entsteht durch Zusammendrücken des Schaums zwischen zwei Platten, wobei der Plattenabstand kleiner sein muss als der Durchmesser der kleinsten Blase. Zweidimensionaler Schaum tritt bei vielen Produktionsprozessen auf und kann sich sehr schnell aufbauen.
© Klaus-Dieter Keller
In welchen Industrien entstehen Probleme mit großen Schaummengen?
Die Schaumbildung in Flüssigkeiten verursacht in verfahrenstechnischen Anlagen häufig Störungen, da der Schaum in Anlagenbereiche vordringt, wo die Flüssigkeit nicht hingelangen soll. Während Oberflächenschaum leicht an den Schaumblasen zu erkennen ist, sind eingeschlossene Luft- oder Gasblasen meist nur an ihren störenden Auswirkungen auf den Betriebsablauf erkennbar.
Papierindustrie
In der Papierindustrie kommt es während des gesamten Produktionsprozesses zu teils extremer Schaumbildung - angefangen von der Zellstoff- bis hin zur Papierproduktion. Der Schaum bewirkt die Hohlsogbildung der Pumpen, verursacht Messfehler bei Levels und Volumen und beeinträchtigt durch Löcher und Fehler im Papier die Qualität des Endproduktes. Bei Anwendungen wie der Papierstreicherei stören Luftblasen den Veredelungsprozess und beeinträchtigen die Strichqualität. Je nach Anlage und Applikation werden daher u.a. passende Entschäumer für die Papierverarbeitung (Leimpresse, Streichmasse), für die Streichfarben und vor allem für die Abwasserbehandlung gebraucht.
Chemische Synthese
Bei der chemischen Synthese (Veresterungen, Umsetzungen, Amidierungen, etc.) ist die Zugabe von Entschäumern im Prozess bei stark schäumenden Rohstoffen erforderlich. Oder auch bei Polymerisationen, da die enthaltenen Netzmittel (Tenside) die Eigenschaft haben, stark zu schäumen.
Fermentation
Die Schaumentstehung bei fermentativen Prozessen zur Herstellung von z.B. Bioethanol, Citronensäure oder Milchsäure ist begründet durch schaumaktive Substanzen in der Fermenterbrühe, entweichende Gase/Luft sowie Turbulenzen im Fermenter. Ebenso können Aminosäuren und Proteine, die von Mikroorganismen während der Fermentation gebildet werden, zu erheblicher Schaumbildung führen. Die Zugabe von Entschäumern verhindert das Überschäumen von Fermentern, was neben dem Verlust von Produktmengen zu erheblichen Verschmutzungen führen würde.
Abwasseraufbereitung & Trinkwasseraufbereitung
Industrieabwässer, Abwässer aus Betrieben und der Landwirtschaft oder Schmutzwasser aus privaten Haushalten enthalten meist oberflächenaktive Substanzen wie Tenside, die Schaum verursachen. Auch können im Zuge der biologischen Reinigung in der Kläranlage durch die Arbeit der Bakterien Gase und infolgedessen Schaum entstehen. Je nach Anwendung sind entsprechende Entschäumer für den aeroben bzw. anaeroben Bereich der Abwasserreinigung wie auch solche für spezielle industrielle Prozessabwässer notwendig.
Farben- und Lackindustrie
Schaum kann bereits bei der Herstellung und beim Abfüllen von Farben und Lacken auftreten und dazu führen, dass die Behälter nicht optimal gefüllt werden können. Die meisten Probleme treten aber bei der Applikation auf. Der Schaum verursacht Oberflächenstörungen und vermindert die Schutzfunktion der Beschichtung. Aus diesen Gründen ist in den meisten Farb- und Lacksystemen ein Entschäumer fester Bestandteil der Formulierung.
Bauindustrie
Beim Trocknen von Zement, Beton, Putzen oder selbstnivellierenden Produkten kommt es durch platzende Schaumblasen zu Schäden wie Löchern und anderen Beeinträchtigungen an der Oberfläche. Um dies zu verhindern, verwendet man Pulver-Entschäumer. Selbstnivellierende Produkte sind deren Hauptanwendung. Sie kommen hauptsächlich in Estrichen zum Einsatz und beinhalten Zement, Kalk, Verdicker, Bindemittel, Superplastisizer, Verzögerer, Beschleuniger und Entschäumer. Der Entschäumer zerstört den Schaum im Vorfeld und wirkt entlüftend. Gleichzeitig verbessert der Entlüfter die Fließfähigkeit des Zementes nach dem Mischen.
Lebensmittelindustrie
In der verarbeitenden Lebensmittelindustrie führen verschiedenste Ursachen zu einer mitunter beträchtlichen Schaumbildung. Störungen der Betriebsabläufe und Verluste erheblicher Produktionsmengen sind die Folge. Entschäumer unterstützen die Prozessstabilität und verhindern Verschmutzungen sowie andere negative Auswirkungen. Eine der größten Herausforderungen für Entschäumer ist zum Beispiel die Zuckerproduktion, da hier der Einsatz von Entschäumern in sämtlichen Prozessschritten erforderlich ist – von der Rübenwäsche bis hin zum Melassetransport.
Die Wirkungsweise von Entschäumern
Der Begriff „Entschäumung“ wird verwendet, um die Entfernung von Gasblasen zu beschreiben. In bestimmten Fällen sollte jedoch eine Unterscheidung zwischen „Entschäumung“ und „Entlüftung“ getroffen werden:
Entschäumer sind nur an der Oberfläche wirksam, wo sie die Schaumblasen destabilisieren und zum Platzen bringen. In diese Kategorie fallen Schaumverhinderer und Schaumzerstörer. Diese bilden an der Grenzfläche der Flüssigkeit einen geschlossenen Film, der das Ausgasen beschleunigt bzw. durch Zerstörung der Gasbläschen ermöglicht.
Entlüfter hingegen führen Gasteilchen zu Blasen zusammen, die in Folge an die Oberfläche steigen und so entweichen können. Schaumentlüfter müssen daher im gesamten Medium ihre Wirkung entfalten und nicht nur an der Oberfläche.
Grundsätzlich lässt sich die Wirkungsweise von Entschäumern somit in drei Klassen einteilen:
- Schaumzerstörung: Ein Entschäumer dieser Klasse zerstört den Schaum an der Oberfläche. Der Schaumzerstörer wird entweder von oben aufgesprüht oder man lässt ihn von oben herabrieseln.
- Schaumverhinderung: Antischaumzusätze haben die Eigenschaft, Schaumformationen sofort abzubauen und eine Neubildung von Schaum zu verhindern. Der Schaumverhinderer wird meist über eine Dosierstelle in das zu entschäumende Medium eingebracht, wobei man sich im Vorfeld gut überlegen sollte, an welcher Stelle man am besten dosiert. Die Auswahl der richtigen Dosierstelle ist außerordentlich wichtig für die optimale Wirksamkeit der Entschäumer.
- Schaumentlüftung: Entschäumer mit einer stark entlüftenden Wirkung sind vor allem für Farb- und Lacksysteme wichtig. Entlüfter beschleunigen die Aufstiegsgeschwindigkeit der Luftblasen (Mikroschaum) in nassen Farben und Lacken, damit die Luftblasen das Medium noch vor der Trocknung verlassen können. Ohne Entlüfter würden z.B. nach dem Auftrocknen einer Korrosionsschutzlackierung winzige Löcher in der Oberfläche entstehen, die erneut eine Angriffsfläche für Korrosion bieten.
Arten und chemische Klassifizierung von Entschäumern
Je nach Zusammensetzung haben Entschäumer eine mehr oder weniger starke entlüftende Wirkung, beugen der Schaumbildung vor oder destabilisieren bestehende Schäume. Generell lassen sich Entschäumer/Entlüfter in vier Hauptgruppen unterteilen:
- Silikonfreie Entschäumer: Entschäumerflüssigkeiten auf Basis von Mineralölen, Polyolen, EO-PO-Blockpolymeren, Fettsäuren/Fettalkoholen, Estern, Ethern, etc.
- Silikonentschäumer: Entschäumerflüssigkeiten mit besonders niedriger Oberflächenspannung, die als Hauptwirksubstanz Dimetylsiloxane in verschiedenen Varianten enthalten. Zusätzlich können auch noch verschiedene Kieselsäuren oder Silikonöle eingebracht werden.
- Andere organische Entschäumer: Entschäumerflüssigkeiten auf Basis einfach definierter organischer Substanzen, die in verschiedenen Anwendungen entschäumende Wirkung entfalten, z.B. Triisobutyphosphat/Tir-n-butylphosphat und andere Phosphatester.
- Pulverentschäumer: Pulverförmige/feste Entschäumer für feste Bauprodukte, die mit Flüssigkeit angerührt werden, wie z.B. Tapetenkleister, Fliesenkleber oder Spachtelmassen.
Nachfolgend eine kurze Übersicht, welche Entschäumer die Donauchem unter der Bezeichnung DonFoamex anbietet und in welchen Anwendungen sie zum Einsatz kommen:
Fazit: Den passenden Entschäumer finden
Welcher Entschäumer für welchen Einsatz geeignet ist, lässt sich nicht generell sagen - das sollte jeweils durch Vorversuche ermittelt werden. In der Abwasseraufbereitung werden beispielsweise Emulsionen verschiedenen Silikongehalts oder nicht silikonhältige lösliche Verbindungen unterschiedlicher Konzentration verwendet. Im Wasch- und Reinigungsmittelsektor wiederum benötigt man Entschäumer unterschiedlichen Silikongehalts sowie verschiedener Viskosität, die als Emulsion, lösliche Verbindung, Pulver, Flüssigkeit usw. auftreten können.
Die Donauchem unterstützt Sie gerne dabei, herauszufinden, welches Produkt jeweils am besten für Ihre Anwendung geeignet ist!
www.donauchem.at