Pulveraktivkohle (PAK) ist eine leistungsstarke Lösung zur Bindung von Schadstoffen. Die Handhabung erfordert jedoch Sorgfalt: Staubbildung, Reinheitsanforderungen und Verdichtung stellen hohe Ansprüche an Transport und Lagerung.
Pulveraktivkohle: Herstellung, Eigenschaften und Anwendungen
Pulveraktivkohle ist ein echtes Multitalent in der Industrie, das in der Lage ist, Schadstoffe wie organische Verunreinigungen, Schwermetalle, Farbstoffe und Gerüche zu adsorbieren. Sie wird vor allem in der Wasseraufbereitung, Lebensmittelindustrie und chemischen Produktion verwendet, um unerwünschte Stoffe aus Flüssigkeiten und Gasen zu entfernen.
Der Herstellungsprozess von PAK umfasst drei wesentliche Schritte:
- Pyrolyse: PAK wird durch Pyrolyse kohlenstoffhaltiger Ausgangsstoffe wie Steinkohle, Braunkohle, Holz oder Kokosnussschalen hergestellt. Dabei wird das Material unter Sauerstoffausschluss erhitzt, um eine kohlenstoffreiche Basisstruktur zu erzeugen.
- Aktivierung: Im Anschluss sorgt eine thermische oder chemische Aktivierung für eine erhöhte Porosität und schafft eine große innere Oberfläche von 500 bis 1.500 m²/g, die der Aktivkohle ihre hohe Adsorptionsfähigkeit verleiht.
- Pulverisierung: Schließlich wird die aktivierte Kohle fein gemahlen, um die charakteristische Pulverform der PAK zu erhalten. Die resultierenden Partikel haben eine Größe von 10 bis 50 Mikrometern (µm) und ein Schüttgewicht von 200 bis 600 kg/m³.
So entsteht ein hochfeines, poröses Pulver mit idealen Eigenschaften für industrielle Filtrations- und Adsorptionsprozesse. Doch so effizient PAK in der Anwendung ist, stellt ihre feine Struktur auch besondere Anforderungen an Handhabung und Transport.
Abbildung 1: Pulveraktivkohle hat eine Größe von 10 bis 50 Mikrometern (µm) und ein Schüttgewicht von 200 bis 600 kg/m³.
Herausforderungen beim Handling von Pulveraktivkohle
Pulveraktivkohle erfordert beim Handling besondere Sorgfalt: Um optimale Sicherheits- und Qualitätsstandards sicherzustellen, müssen Staubentwicklung, die Vermeidung von Kontaminationen und das Schüttgewicht der PAK beachtet werden.
1. Vermeidung von Staubentwicklung
Die feine Struktur und das geringe Gewicht von PAK führen leicht zu Staubbildung – schon ein leichter Luftzug genügt, um das Pulver in der Luft zu verteilen und als feinen Staub abzusetzen. Dabei fluidisiert der Staub, d. h. er verhält sich wie eine Flüssigkeit und haftet mühelos an fast allen Oberflächen. Bei Kontakt mit einer Zündquelle kann aufgewirbelte PAK sogar Staubexplosionen auslösen. Beim Befüllen und Entleeren sind daher technische Maßnahmen zur Staubvermeidung sowie entsprechende Sicherheitsvorkehrungen zwingend erforderlich.
2. Sicherstellung der Kontaminationsfreiheit
PAK kommt oft in sensiblen Anwendungen zum Einsatz, bei denen Reinheit eine hohe Priorität hat (z. B. in der Wasseraufbereitung). Unsachgemäßes Handling kann dazu führen, dass Verpackungsteile oder andere Fremdkörper in die Pulveraktivkohle gelangen, die erhebliche Probleme beim Verbraucher verursachen können. Um dem vorzubeugen, werden oft Siebe eingesetzt, sowohl beim Beladen von Tankwagen aus Big Bags oder Silos als auch beim Kunden während des Entladungsprozesses.
3. Berücksichtigung des Schüttgewichts
Eine häufige Fragestellung bei Pulveraktivkohle betrifft das Schüttgewicht (auch Schüttdichte). Es beschreibt das Gewicht lose geschütteter Aktivkohle pro Volumeneinheit (meist in kg/m³) und ist von Faktoren wie Partikelform, -größe und -verteilung beeinflusst. Während die Schüttdichte granularer Aktivkohle aufgrund ihrer stabilen Partikelstruktur relativ konstant bleibt, gestaltet sich die Messung bei PAK schwieriger:
Wie jedes andere Pulver verdichtet sich PAK leicht, wodurch sich das Schüttgewicht verändern kann. Besonders in Silowagen und Verbrauchersilos führt der Druck der oberen Schichten zur Kompression der unteren und erhöht die Schüttdichte mit steigender Füllhöhe – ein Effekt, der in Transport-, Lager- und Dosierprozessen berücksichtigt werden muss.
Transportoptionen für Pulveraktivkohle
Pulveraktivkohle wird üblicherweise in
Big Bags oder kleineren
Poly- oder Papiersäcken verpackt, die sich gut für Lagerung und Transport per Lkw, Bahn, Flugzeug und besonders für den Seetransport eignen. Eine Alternative für den Transport großer Mengen Aktivkohle sind
Silowagen, die das Material direkt zum Verbraucher bringen und dort meist in Silos entleeren.
Für das Beladen der Silowagen gibt es verschiedene Systeme: In den meisten Fällen wird die Aktivkohle über die oberen Mannlöcher eingefüllt. Dabei kommt oft ein Kran zum Einsatz, der das Big Bag freischwebend über dem Silowagen positioniert, sodass die Kohle durch das Öffnen des Entleerungsstutzens einfach hineinfällt. Alternativ kann die Beladung auch direkt aus stationären Silos erfolgen, unter die der Silowagen fährt, oder über einen Rohrkettenförderer, der die Aktivkohle nach oben transportiert und über einen Trichter in den Silowagen entleert.
Abbildung 2: Tankwagen verfügen über spezielle Anschlüsse und Systeme, die eine effiziente Handhabung der Pulveraktivkohle ermöglichen.
Sichere Entladung von Pulveraktivkohle beim Kunden
Bei der Entladung von Pulveraktivkohle kommt es auf einen sicheren und kontrollierten Materialfluss an. Ob aus Silowagen, Big Bags oder Säcken – jedes Entladesystem bringt spezifische Anforderungen mit sich, um Staubbildung und Verklumpungen zu minimieren.
1. Entladung von Silowagen
Nach der Anlieferung im Silowagen wird die Pulveraktivkohle meist mithilfe von Druckluft in das vorgesehene Silo eingeblasen. Je nach Bedarf kommen dabei verschiedene Systeme zum Einsatz, von einfachen Rohrleitungen bis hin zu komplexen pneumatischen Förderanlagen. Um die eingepresste Luft entweichen zu lassen und gleichzeitig die Aktivkohle im Silo zu halten, sind Silos mit speziellen Belüftungseinrichtungen ausgestattet.
Bei der Entladung in Silos sind vor allem zwei Aspekte zu beachten:
- Sicherheitsreserve von etwa 10 Prozent: Wie bereits erwähnt, verändert sich das Schüttgewicht der Pulveraktivkohle durch Verdichtung. Um die Materialbewegung zu optimieren und unvorhergesehenen Druckaufbau im Silo zu verhindern, wird empfohlen, das Silo nur bis maximal 90 % seiner theoretischen Kapazität zu befüllen.
- Ausreichend Befüllzeit einplanen: Damit sich das Material im Silo gleichmäßig setzen kann, sollte beim Befüllen ausreichend Zeit eingeplant werden. Andernfalls können Hohlräume oder Luftblasen entstehen, die später die Entnahme erschweren.
Wird das Silo zu schnell befüllt oder fehlt eine ausreichende Reserve, kann es zur
Brückenbildung kommen. Dabei verdichtet oder verklumpt die Pulveraktivkohle so stark, dass sie eine stabile „Brücke“ über dem Austragsbereich bildet. Infolgedessen wird die Kohle ungleichmäßig und nicht kontinuierlich dem Dosiersystem zugeführt.
Um Brückenbildung zu vermeiden, setzen Betreiber häufig Vibrationsaustragsböden, Fluidisierungsluftsysteme, Rüttelvorrichtungen oder mechanische Rührwerke ein. Brückenbildung ist jedoch nicht nur auf Silos beschränkt, sondern kann auch in Vorlagebehältern, Förderanlagen oder Rohrleitungen auftreten.
Abbildung 3: Bei der Befüllung von Silos mit Pulveraktivkohle sollten eine Sicherheitsreserve von ca. 10 % der Kapazität sowie ausreichend Befüllzeit eingeplant werden, um die Entstehung von Hohlräumen oder Brückenbildung zu vermeiden.
2. Entleerung von Big-Bags und Säcken
Säcke und Big Bags werden über spezielle Entleerungssysteme in Lagereinrichtungen wie Silos und Container oder direkt in Vorlagebehälter, Dosieranlagen oder Fördermechanismen entleert – je nach Produktionsanforderung. Die Entladestationen sind mit Zusatzeinrichtungen ausgestattet, die eine vollständige Entleerung sowie eine luftdichte Verbindung zum Aufnahmebehälter sicherstellen.
Für die Entleerung von Säcken kommen häufig manuelle Sackaufgabestationen mit Staubhauben und integriertem Sieb zum Einsatz. Patronenfilter und Absauganlagen minimieren Staubemissionen und halten den Arbeitsbereich sauber. Zusätzlich ist meist ein Sackverdichter angeschlossen, der leere Säcke kompakt entsorgt und so Abfallvolumen und Staubbelastung reduziert.
Big Bags werden in der Regel über spezialisierte Entleerstationen mit Füllschleusen entleert, die den Auslass des Big Bags sicher verschließen. Dichtmanschetten und Absaugvorrichtungen oder Staubabscheider sorgen für eine staubfreie Materialübertragung in den Zielbehälter oder das Fördersystem. Das Siebsystem ist hier oft am Auslass der Big-Bag-Entladevorrichtung integriert.
Anwendung von Pulveraktivkohle beim Verbraucher
Pulveraktivkohle lässt sich flexibel dosieren und an verschiedene Anforderungen anpassen. Sie ermöglicht eine ressourcenschonende Nutzung, besonders in Anlagen, die auf schwankende Schadstoffkonzentrationen schnell reagieren müssen. Im Unterschied zu granularer oder pelletierter Aktivkohle, die als Filterbett eingesetzt wird, kann Pulveraktivkohle direkt in das Medium eingetragen werden.
1. Eindüsungsverfahren
Bei der Luft- und Gasreinigung kommt häufig das Eindüsungsverfahren zum Einsatz. Dabei wird pulverförmige Aktivkohle direkt über Düsen in den Gasstrom eingeblasen, wo sie sich gleichmäßig verteilt und Schadstoffe während des Durchströmens adsorbiert. Anschließend wird die beladene Aktivkohle durch spezialisierte Filtersysteme wieder entfernt.
Lesen Sie auch: Rauchgas: Reinigung mit Aktivkohle gegen Quecksilber & Co.
2. Einrühr- oder Suspensionsverfahren
Das Einrühr- oder Suspensionsverfahren ist die häufigste Methode zur Reinigung von Flüssigkeiten und in der Wasseraufbereitung. Dabei wird die Aktivkohle entweder trocken in die Flüssigkeit gemischt oder als 15%-ige Suspension zugegeben. Für die Herstellung der Suspension kann Wasser, Kondensat oder bereits gereinigte Lösung verwendet werden. Ihr Vorteil liegt in der Vermeidung von Verklumpungen, die die Adsorptionsleistung beeinträchtigen könnten.
Nach der Adsorption wird die beladene Aktivkohle entweder abgetrennt oder in einem Rezirkulationsprozess erneut genutzt, da oft noch Restkapazität vorhanden ist. Die verbleibende Kapazität lässt sich bei Mehrfachanwendungen optimal nutzen, um die stark verunreinigte Ausgangslösung mit bereits gebrauchter Aktivkohle vorzureinigen, bevor sie anschließend mit frischer Aktivkohle behandelt wird.
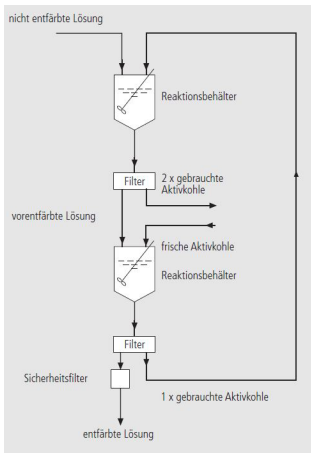
Abbildung 4: Zweistufige Anwendung pulverförmiger Aktivkohlen
3. Anschwemm- oder Schichtenfiltrationsverfahren
Eine weniger verbreitete Methode zur Reinigung von Flüssigkeiten ist das Anschwemm- oder Schichtenfiltrationsverfahren, bei der eine Schicht aus Aktivkohle auf einem Filterelement aufgebracht wird, durch die die Flüssigkeit gefiltert wird. Das Verfahren eignet sich besonders für geringere Verunreinigungskonzentrationen und ermöglicht zusätzlich die Entfernung partikulärer Verunreinigungen.
Lesen Sie auch: Raffination von Speiseöl: der Vorteil von Aktivkohle
Fazit: Handhabung von Pulveraktivkohle
Die Handhabung von Pulveraktivkohle erfordert Maßnahmen zur Staubvermeidung, Berücksichtigung des variablen Schüttgewichts und Sicherstellung der Kontaminationsfreiheit. PAK ist sehr fein und leicht, wodurch bei Bewegung oder Luftzug Staub entsteht. Der Staub kann sich schnell verteilen, an Oberflächen haften und bei Zündung explosionsgefährlich sein. Ebenso wichtig ist der Schutz vor Fremdkörpern und die Berücksichtigung der Schüttdichte bei Transport und Lagerung.