In einer vernetzten und digitalisierten Welt funktioniert ohne Halbleiter nichts mehr – Chips sind das neue Öl der Weltwirtschaft. Doch obwohl die Nachfrage nach Halbleitern enorm boomt, schaffen es die Hersteller nicht, die Nachfrage zu bedienen. In Fortsetzung unseres Blogs
Warum Donauchem einen Fokus auf Chemikalien für die Leiterplattenherstellung setzt beleuchten wir in diesem Beitrag die aktuelle Situation in Hinblick auf Rohstoffverfügbarkeit und andere relevante Einflussfaktoren.
Weiters geben wir einen Ausblick auf die prognostizierte Entwicklung der Halbleiterindustrie und damit verbundener Branchen.
Halbleiter Markt: Wachstumsrate von 25 Prozent in 2021
Bislang kalkulierte die Chipbranche mit einem jährlichen Umsatzwachstum von bis zu fünf Prozent. Nach einem Wachstum von 6,8 Prozent im Jahr 2020 erwartet der Branchenverband
World Semiconductor Trade Statistics (WSTS) für 2021 ein Wachstum des weltweiten Halbleitermarkt auf 551 Milliarden US-Dollar.
Dies entspricht einer globalen Wachstumsrate von 25,1 Prozent für 2021. Die größten Wachstumstreiber sind Speicher mit 37,1 Prozent, gefolgt von Analog-Chips mit 29,1 Prozent und Logik-Chips mit 26,2 Prozent. Europa wird sich laut diesen Prognosen 2021 mit einem Marktwachstum von 26,4 Prozent erholen.
Für das Jahr 2022 gehen Analysten von einem Wachstum des weltweiten Halbleitermarktes um 10,1 Prozent auf 606 Milliarden US-Dollar aus. Haupttreiber ist die Kategorie Speicher mit einem zweistelligen Wachstum. Europa wird 2022 voraussichtlich eine positive Wachstumsrate von knapp 8 Prozent aufweisen.
Halbleiter bestehen hauptsächlich aus vier Komponenten: Diskreten Halbleitern, optoelektronischen Geräten, Sensoren und Integrierten Schaltkreisen (IC). Integrierte Schaltungen machen mehr als 80 Prozent der Geräte aus und werden wiederum nach vier Produkttypen kategorisiert: Analoge Geräte, Mikroprozessoren, Logikgeräte und Speicher. Chips ist der gebräuchliche Oberbegriff dieser IC-Kategorien.
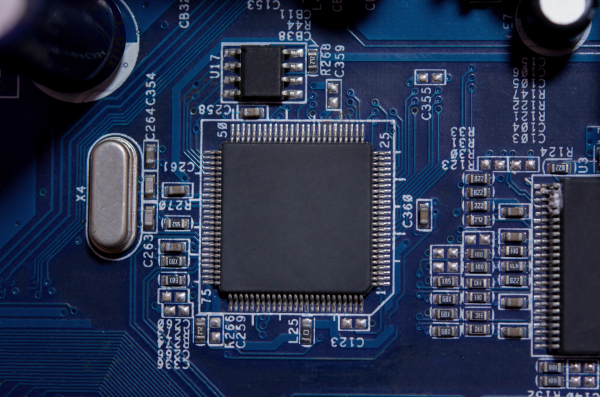
Abb.: Eine Leiterplatte bzw. Platine besteht aus verschiedenen Halbleitern, deren einzelne Funktionen komplexe Systeme ermöglichen.
Intensivierung der schlechten Rohstoffversorgung für Halbleiter
Ein Halbleiter-Chip setzt sich im Wesentlichen aus integrierten elektronischen Schaltkreisen (IC) zusammen, die auf einer kleinen Siliziumscheibe, dem sogenannten Wafer, aufgebracht sind. Je nach Halbleiter-Typ sind für die Herstellung 400 bis 1400 Schritte sowie rund 300 bis 400 verschiedene Chemikalien erforderlich. Zum anderen sind 50 verschiedene Arten von Fertigungsmaschinen notwendig.
Die anhaltende Rohstoffverknappung beeinträchtigt die Produktion für eine Vielzahl von Komponenten, wodurch es vor allem zu Engpässen bei ICs, CPUs und Speichern kommt:
Die Materialbasis für Halbleiter ist in erster Linie hochreines Silizium, welches wiederum das ABF-Substrat für die weitere Chip-Fertigung benötigt. ABF-Substrate sind gegenwärtig die dominierende Technologie für die Anwendung im Bereich von Hochleistungs-Prozessoren. Da die Kapazitätsgrenze der Substratfertigungsanlagen erreicht ist, gehen Analysten davon aus, dass die Verknappung bis 2023 andauern wird.
Zusätzlich zum Substrat-Engass sind Halbleiter von einem globalen Engpass von 8-Zoll-Wafern betroffen. In den vergangenen zehn Jahren sind vor allem Fabriken für moderne 12-Zoll-Wafer entstanden. Viele Halbleiter benötigen aber kleinere Siliziumscheiben. Im Zuge der hohen Nachfrage fehlt es nun an Maschinen, um 8-Zoll-Wafer zu verarbeiten. Hersteller weichen daher soweit als möglich auf gebrauchte Maschinen aus, die Lieferzeit für neues Equipment liegt derzeit bei bis zu einem Jahr.
- Rohstoffe für Kunststoffproduktion
Neben Engpässen bei Chemikalien für die Oberflächenbehandlung von Leiterplatten wie
Kaliumperoxomonosulfat und hochreine
Salzsäure, gibt es auch Einschränkungen bei Chemikalien, die zur Herstellung von Kunststoffen verwendet werden.
Bestimmte Kunststoffe werden auch in der Produktion von Halbleitern benötigt, z. B. für Leiterplatten, elektrische Isolatoren, Reinstwassersysteme und Nassbänke, um nur einige zu nennen. Wenn diese Kunststoffe weiterhin knapp bleiben, können viele Halbleiter nicht mehr produziert werden.
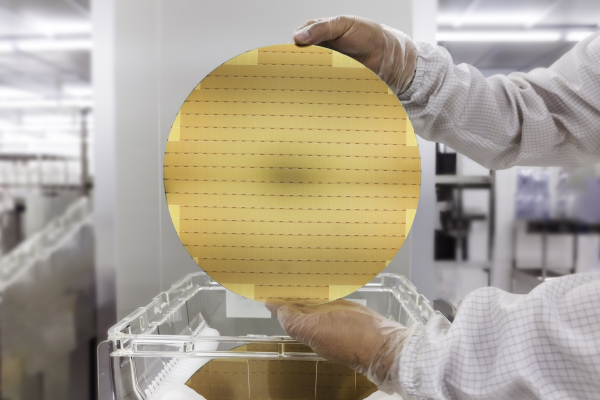
Abb.: Silicium Wafer, der für die Chipproduktion vorbereitet wird.
Chipmangel führt zu Preissteigerungen um bis zu 20 Prozent
Die Chip-Vorräte sind derzeit auf einem historischen Tiefstand. Chips gehen nach der Fertigstellung direkt in die Produktion der Endanwendungen. Manager großer Halbleiterhersteller wie Intel-Chef Pat Gelsinger und Infineon-CEO Reinhard Ploss gehen davon aus, dass die Lieferengpässe bis weit ins nächste Jahr hinein andauern werden, wenn nicht sogar darüber hinaus.
Mehrere Hersteller haben bereits angekündigt, die Chip Preise um 10 bis 20 Prozent anzuheben. Die Hauptursachen dafür sind neben der Verfügbarkeit von Rohstoffen in Elektronik-Qualität in folgenden Faktoren zu finden:
Hohe Nachfrage und Kryptowährung-Boom
Das konstante Nachfragewachstum verschiedener Sektoren wie 5G, Automotive und IoT stellt eine der Hauptursachen des Chipmangels dar. Zudem gab es 2021 einen deutlichen Anstieg von Krypto-Mining-Aktivitäten. Infolgedessen wurde das globale Angebot an Halbleitern zusätzlich unter Druck gesetzt. GPU- und Speicherhersteller beginnen bereits damit, Produkte zu entwickeln, die auf Mining-Anwendungen fokussieren.
Zu wenige Fabriken durch Konsolidierung in der Branche
Die Herstellung eines Halbleiters läuft in drei Stufen ab: Zunächst erfolgt die technische Gestaltung, das Design, dann die Fertigung, schließlich das Gehäuse und Anbringen von Kontakten, das sogenannte Packaging. Die Konsolidierung innerhalb der Branche hat nun dazu geführt, dass nur eine Handvoll Unternehmen Fabs betreiben. Denn viele Chipfirmen konzentrieren sich lediglich auf das Design und überlassen die Produktion ihrer Designs diesen großen Herstellern.
Spezialisierung bringt zwar Wettbewerbsvorteile, bedeutet aber auch, dass Halbleiterunternehmen stark voneinander abhängig sind. Laut
McKinsey verfügt kein lokaler Markt und kein lokales Unternehmen über alle Kompetenzen, die für durchgängiges Halbleiterdesign und -fertigung erforderlich sind. Der Anteil der Weltregionen (in %) an den Umsätzen in der Wertschöpfungskette zeigt dies sehr anschaulich:
Quelle:
Gartner, IHS, Strategie-Analyse McKinsey
Ungleiche Technologieentwicklung
Eine entscheidende Ursache für die aktuellen Engpässe scheint auch in der ungleichen Technologieentwicklung im gesamten Ökosystem zu liegen. Dies bedeutet nicht nur, dass sich einige Regionen auf bestimmte Technologien spezialisieren, sondern es gibt auch eine Diskrepanz zu einigen Ländern, die ältere Verfahren zur Chipherstellung verwenden. Diese technologische Ungleichheit zwischen den weltweiten Standorten birgt die Gefahr einer erheblichen Unterbrechung der Lieferkette, wie es während der Covid-19-Krise der Fall war. Es macht daher keinen Sinn, nur die Kapazität in bestimmten Regionen zu erhöhen. Es müssen langfristige, globale Lösungen gefunden werden.
Konflikt China - USA
Ein weiterer Grund für den weltweiten Chipmangel ist im Konflikt zwischen China und den USA zu finden. Die Drohung des früheren US-Präsidenten Donald Trump, China mit Sanktionen zu belegen, führte zu Hamsterkäufen der chinesischen Tech- und Elektronikbranche. Als Folge kam die die Just-in-time-Produktion großer internationaler Konzerne komplett aus dem Takt.
Naturkatastrophen und coronabedingte Lieferkettenprobleme
Coronabedingte Lieferkettenprobleme und unvorhergesehene Naturkatastrophen setzen der Halbleiterindustrie weiterhin zu. Wichtige Länder der Halbleiterproduktion wie Ostchina, Malaysia, Vietnam, Thailand, die Philippinen und Singapur sind mit Disruptionen durch Corona-Ausbrüche, Überschwemmungen und Taifune konfrontiert. Taiwan hat darüber hinaus mit den Auswirkungen der schlimmsten Dürre seit mehr als einem halben Jahrhundert zu kämpfen.
Taiwan nimmt mit fast zwei Drittel der globalen Kapazitäten für die Auftragsfertigung eine herausragende Stellung ein. Große Hersteller wie TSMC, UMC, Winbond und Samsung sind mit ihren Fabriken auf der Insel angesiedelt. TSMC ist der weltweit größte Produzent von Microcontrollern, die in der Autoindustrie besonders fehlen.
In welchen Branchen fehlt es am meisten?
Chips mit integrierten Schaltkreisen (ICs) sind Teil aller Geräte und Maschinen, die über ein gewisses Maß an Mikroprozessorsteuerung verfügen. Zahlreiche Technologien funktionieren ohne sie einfach nicht. Die Lieferengpässe bei Halbleitern belasten daher weltweit viele Industriezweige. Eine der stärksten betroffenen Branchen ist die Automobilindustrie. Aber auch Computer- und Handyproduzenten oder Hausgerätehersteller haben inzwischen mit dem fehlenden Nachschub an elektronischen Bauteilen zu kämpfen.
Kurzfristige Erholung der Automobilindustrie unwahrscheinlich
Nachdem die Autoindustrie während der Corona-Lockdowns 2020 ihre Bestellungen reduzierte und 2021 rasch wieder erhöhte, kam es zu ersten Engpässen bei Mikrochips. Der Brand in einer für die Autoindustrie wichtigen Chipfabrik in Japan bremste dann im Frühjahr 2021 die Autoproduktion erneut weltweit aus, insbesondere in Europa und den USA.
Mittlerweile müssen die Autobauer trotz voller Auftragsbücher auf Kurzarbeit umsteigen, ihre Bänder wochenweise anhalten oder komplett stillegen. Ferdinand Dudenhöffer vom Center Automotive Research (CAR) in Duisburg schätzt, dass aufgrund des Halbleitermangels dieses Jahr weltweit 5,2 Millionen Fahrzeuge weniger gebaut werden als geplant. Darüber hinaus erwartet der Autoexperte bis zum Jahr 2030 Lieferprobleme in der Automobilproduktion.
Verantwortlich dafür macht er einerseits die Halbleiterknappheit, die sich bis zum Beginn des Jahres 2023 auswirken wird, sowie anschließend Probleme bei der Verfügbarkeit von Batteriezellen. Für das Jahr 2026 prognostiziert Dudenhöfer eine weltweite Nachfrage von 90 Millionen Fahrzeugen. Die Hersteller können seinen Daten zufolge dann aber nur 85,6 Millionen Autos produzieren.
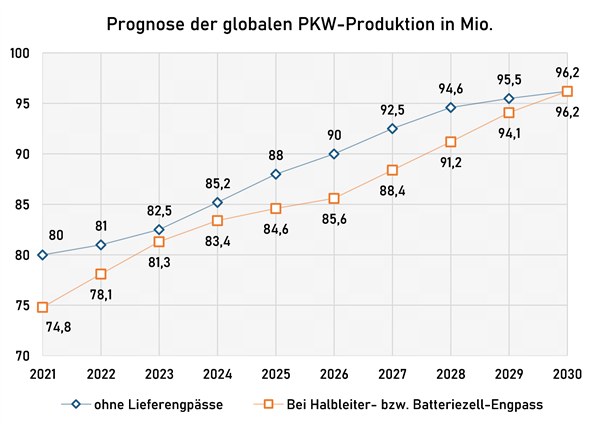
Quelle:
CAR Duisburg
Der deutsche Unternehmensberater PwC beurteilt die Produktionspläne der Autoindustrie angesichts der Halbleiterkrise ebenfalls äußerst skeptisch. Der Ausbau von Halbleiter-Produktionsanlagen dauere bis zu zwei Jahre, der Bau neuer Werke sogar fünf Jahre - deshalb erwarte man keine rasche Erholung der Versorgung mit Halbleitern.
Produktionsausfälle bei Computer, IoT-Geräten und Weisser Ware
Neben Autobauern müssen auch Mobiltelefon-Hersteller ihre Produktion wegen des Chipmangels zurückfahren – mit Ausnahme des Apple Konzerns, der sich rechtzeitig mit Halbleiterkomponenten eingedeckt hat. Produzenten konzentrieren sich daher aktuell auf Flaggschiff-Geräte und 5G-fähige Smartphones, bei günstigen Geräten drohen hingegen Engpässe. Samsung und Xiaomi stoppen bereits die Herstellung und den Verkauf von Mittelklasse- und Billig-Smartphones in einigen Märkten.
Ebenso sind wegen des Chipmangels Spielekonsolen ein dreiviertel Jahr nach ihrem Erscheinen kaum erhältlich. Lieferprobleme aufgrund von Halbleitermangel sind mittlerweile auch bei Laptops, Druckern, WLAN-Routern, E-Bikes und Haushaltsgeräten deutlich spürbar. Letztlich ist vom Chipmangel die gesamte "Weiße Ware" betroffen. Da viele Unternehmen auf Lager produziert haben, dürften bestimmte Haushaltsgeräte zeitverzögert zu Weihnachten besonders knapp werden.
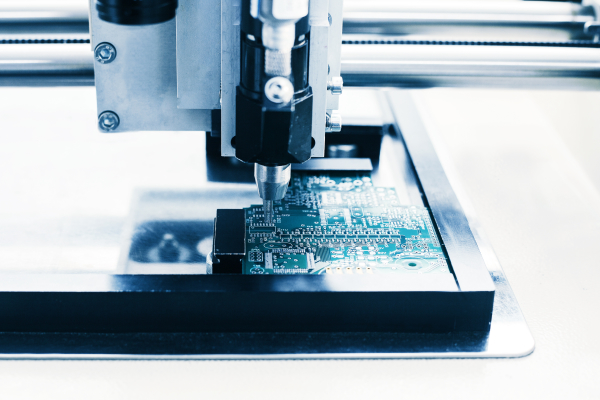
Abb.: Automatisiertes Herstellungsverfahren von Platinen/Mikrochips für Elektronik oder Computer.
Europäische Chip-Industrie hinkt bis zu 15 Jahre hinterher
Die Abhängigkeit Europas von amerikanischen und asiatischen Chipherstellern wird sich so schnell nicht ändern. Europäische Chip-Unternehmen kommen lediglich auf einen Weltmarktanteil von zehn Prozent und hinken in vielen Bereichen um Jahre hinterher. Nach Angaben einer Studie der Unternehmensberatung McKinsey wird es mindestens zehn Jahre dauern, bis Europa an die Weltspitze anschließen kann.
Um auf den fortschrittlichsten Stand der Fertigung zu kommen, rechnet McKinsey mit bis zu 15 Jahren Vorlaufzeit. Eine Ausnahme würden hier lediglich Leistungshalbleiter (Infineon) und Sensorik (Bosch, ST Microelectronics, Infineon) bilden. In diesen Bereichen nimmt Europa eine weltweit führende Rolle ein, mit einem Vorsprung von drei bis fünf Jahren auf Asien und USA.
Neue Chip-Fabriken: Lange Bauzeiten und viel Geld
Die Auslastung vieler Fabriken lag schon vor dem Nachfrageboom bei 80 bis 90 Prozent, da alles darunter unwirtschaftlich ist. Das ist auch der Grund, warum derzeit die Fabs am Anschlag laufen. Der Bau einer neuen Chipfabrik - wie sie die großen Hersteller in Asien und den USA betreiben - kostet etwa 10 bis 15 Milliarden Euro und dauert mehrere Jahre. Zudem müssen zwischen 3.000 und 6.000 Mitarbeiter rekrutiert und ausgebildet werden. Neue Fabriken können somit nur aus langfristiger Perspektive eine Entlastung des Chipmangels bringen.
Halbleiterhersteller prüfen deshalb auch sehr genau, ob und wieviel sie trotz des Nachfragebooms in neue Fabs investieren. Gerade in einer Pandemie sind damit hohe Risiken verbunden. Denn obwohl die Nachfrage hoch ist, können Maschinen für weniger nachgefragte Chips stillstehen. So verzeichnete etwa Infineon vergangenes Geschäftsjahr Leerstandskosten von 600 Millionen Euro.
Dasselbe gilt für Chemikalien-Hersteller, die ihre Fertigungskapazitäten auch nicht von heute auf morgen erhöhen können. Verschärfend wirkt sich aus, dass es nur eine begrenzte Anzahl von Lieferanten für Chemikalien in hochreiner Elektronik- bzw. Semiconductor Grade Qualität gibt. Außerdem beliefern viele der Chemikalien-Zulieferer nicht nur den Halbleiter-Markt, sondern eine Vielzahl von Kunden anderer Branchen. Nur weil die Chip Nachfrage vorübergehend boomt, bauen diese Produzenten kein neues Werk.
Die Hindernisse, neue Fabriken zu bauen, sind also hoch. Der Automobil-Zulieferer Bosch hat es dennoch gewagt und im Juni 2021 in Dresden eine Chip-Fabrik eröffnet, die vor allem den eigenen Bedarf sichern soll. Rund eine Milliarde hat das Unternehmen in die
AIoT-Fabrik investiert.
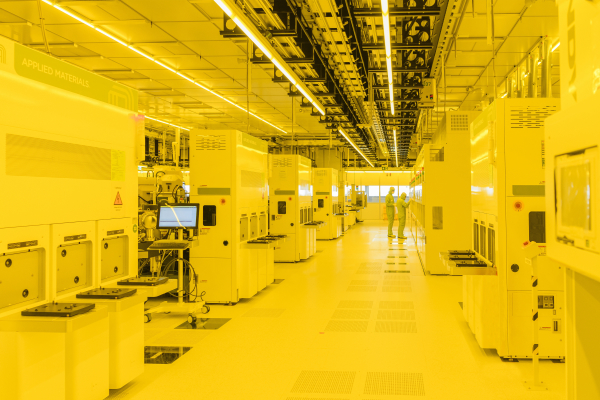
Abb.: Halbleiterfertigung von Bosch in Dresden: Die Beleuchtung des Reinraums besteht aus speziellem Gelblicht, das keine UV-Strahlen enthält. Dadurch wird verhindert, dass die mit Fotolack beschichteten Wafer unbeabsichtigt belichtet werden. Foto: Bosch
Nach drei Jahren Vorbereitungs- und Bauzeit ist Anfang August nun auch in Villach die neue
Infineon High-Tech-Chipfabrik für Leistungselektronik auf 300- Millimeter-Dünnwafern in Betrieb gegangen. Die Chipfabrik ist eine der modernsten weltweit und setzt als „lernende Fabrik“ auf Vollautomatisierung und Digitalisierung. Die Chips decken in der ersten Ausbaustufe vor allem die Nachfrage der Automobilindustrie, Rechenzentren und erneuerbaren Energiegewinnung aus Solar- und Windkraft. In den kommenden vier bis fünf Jahren soll die Fertigung sukzessive hochgefahren werden.
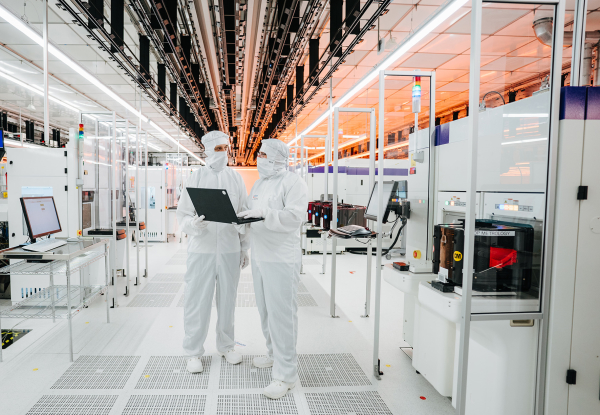
Abb.: Ein Einblick in den Reinraum der neuen High-Tech Chipfabrik in Villach. Bild: Infineon
Infineon geht aber durch Vernetzung der Standorte Villach und Dresden noch einen Schritt weiter. Beide Standorte produzieren 300-Millimeter-Dünnwafer und basieren auf den gleichen standardisierten Fertigungs- und Digitalisierungskonzepten. Damit kann Infineon die Fertigungen der beiden Standorte so steuern, als wären sie eine Fabrik. Steigerung der Produktivität und zusätzliche Flexibilität für Kunden sind die unschlagbaren Vorteile dieser virtuellen Megafabrik.
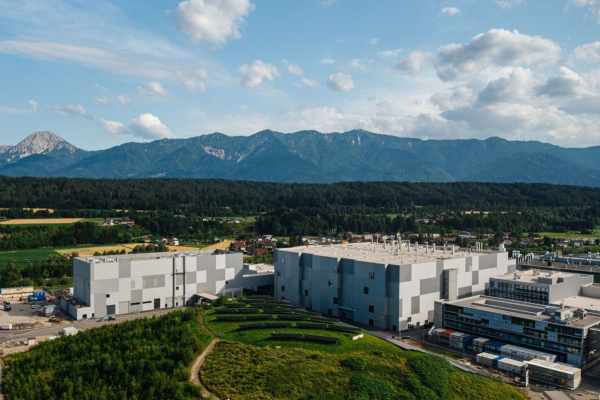
Abb.: 1,6 Milliarden Euro wurden in den Bau der neuen Infineon High-Tech Chipfabrik in Villach investiert. Bild: Infineon
Investitionsprogramm für Europa in den Startlöchern
Um die Position Europas bei der Halbleiterproduktion zu stärken, soll unter anderem der Aufbau neuer Chip-Fabriken mit 145 Milliarden gefördert werden. Die EU-Kommission will damit Europas Weltmarktanteil in den kommenden Jahren von 10 Prozent auf 20 Prozent anheben.
Das US-Unternehmens Intel plant bereits acht hochmoderne Chip-Fabriken in Europa. Rund 30 Prozent der erforderlichen Investition von 80 Milliarden Euro sollen durch öffentliche Beihilfen gedeckt werden. Neben Europa legt auch die USA 50 Milliarden Dollar schweres Programm zur Förderung der heimischen Chipindustrie auf. Staatliche Zuschüsse gibt es seit Jahren auch in Ländern wie Taiwan, Südkorea und vor allem China.
Halbleiterexperten wie McKinsey sprechen sich allerdings deutlich gegen milliardenschwere Investitionen in hochmoderne Halbleiterwerke in Europa aus. Es sei Geldverschwendung, die modernsten Produktionsverfahren in der EU aufzubauen. Stattdessen sollte die EU die Produktion jener Chips fördern, die von der europäischen Industrie tatsächlich gebraucht werden – und das seien nicht High-End Chips.
Intels neueste, hochmoderne Produktionsstätte in Ocotillo, Arizona. Bild: Intel Corporation
Das Fazit: Schnelle Besserung ist nicht in Sicht
Es sieht leider derzeit nicht so aus, als würde der Rohstoff- und Chipmangel in absehbarer Zeit enden. Europäische Hersteller, die auf Lieferungen von qualitativ hochwertigen Rohstoffen und Halbleitern aus Übersee angewiesen sind, empfiehlt es sich daher, die Robustheit ihrer Lieferketten zu erhöhen. Eine mögliche Option ist die höhere Diversifizierung und verstärkte Regionalisierung der Lieferkette in Bezug auf Chemikalien- und Halbleiter-Zulieferer. Ebenso kann eine Neubewertung sinnvoll sein, ob die Lagerhaltung kritischer Rohstoffe und Vorprodukte dem Just-in-time Geschäftsmodell vorzuziehen ist.
www.donauchem.at
Weiterführende Links/Quellen:
Kein Chip wird kommen - Falter 37/21 vom 15.September 2021
Analoge Halbleiter als wertvoller Schatz - Orf.at vom 04.Jänner 2022
Ambitionierte Pläne sollen Chips in die EU holen - Ort.at vom 09.Februar 2022