At the Pischelsdorf site, Donauchem fills, mixes, dilutes and stores a wide variety of chemicals. Production manager Ing. Manuel Blaha and our foremen Roland Zehetner and Dilshad Zangana give you an insight into the production processes, how the many different areas work together and what tasks have to be performed every day.
Ing. Manuel Blaha: Head of Production/Technology
Dilshad Zangana: Foreman solvent area
Roland Zehetner: Foreman Acid/Lye Area
We rely on a strong team
The production plant of Donauchem in Pischelsdorf comprises two separate buildings connected by a glass bridge. In one of these buildings, solvents are mixed and filled, while the other is used for the filling of delivered acids and alkalis and the production of mixtures. For safety reasons, the filling area of the acid and alkali buildings is divided into an acid area, alkali area and mixing area. This is to prevent chemical reactions in the event of a substance leakage.
A total of 21 staff are employed in the filling, mixing and tanker loading and unloading areas. In order to maintain the flexibility to deliver even short-term and above-average orders on time, the teams of the different areas work very closely together. "Our employees are trained to be able to step in wherever someone is needed," says Roland Zehetner. "This flexibility is one of our strengths at our location."
For example, female employees from the labelling department support the bottlers, who in turn support the labellers when there is a need. At peak times, employees also switch to other production areas. "We are in two different buildings, but when there is a lot of work on one side, the employees support each other. When the order situation is high, everyone helps together," explains Ing. Blaha.
21 storage tanks for deliveries of raw materials
An important area of production is tanker loading and unloading. At the unloading point, production workers either take the delivered acids, alkalis and solvents directly or pump them into a storage tank. Special safety regulations must be observed here, which we describe in detail in the article Safety during tanker unloading.
Before unloading begins, the products undergo quality control. "A sample is taken of every raw material delivered before it is decanted to ensure that no defective product is filled into our tanks," explains Roland Zehetner.
For the delivery of acids, alkalis and solvents, there are 21 storage tanks with 30 m3 each. Production staff can fill directly from these tanks or transfer products for mixing into mixing tanks. Several times a day, trucks are also loaded with 2 to 8 tonnes of our products for customers at the loading station.
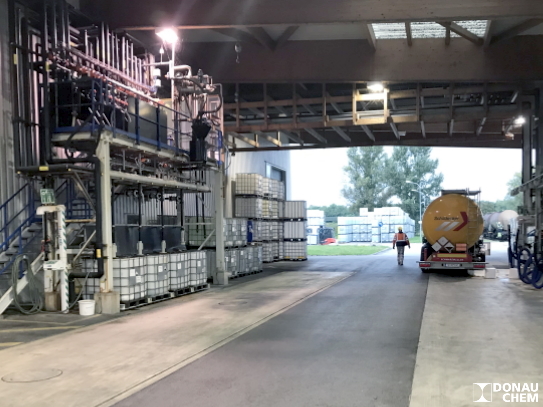
Donauchem tanker unloading station
170 full truckloads leave the plant every month
The storage area in Pischelsdorf currently covers 12,000 m2 and accommodates 14,000 pallet spaces in high-bay racks. In addition, there is a tank capacity for solvents, acids and alkalis of around 2,800 m3. The table below illustrates the monthly warehouse movements - from incoming goods to stock transfers within the warehouse. Storage units can be individual canisters, drums, pallets or IBCs.

© Donauchem
Good planning guarantees smooth processes in productio
After Customer Service has entered a customer order in the system, the production planning department schedules the order in SAP. In the course of production planning, the filling times of the individual products must also be taken into account with regard to their viscosity. There are master recipes for this, which are created for each product.
"After all, we have not only pleasant but also very viscous products. Filling can take several hours. We also have to fill very foaming products very slowly, because otherwise we would have a foam party in production," explains Ing. Blaha. "The many years of experience of our bottlers regarding the use of the right filling equipment and compliance with work instructions plays an important role here."
The tasks of the work preparation department also include updating the production plan on a daily basis. It serves as an orientation for the production areas and as a support for the empty container area in the warehouse: production employees receive a detailed overview of the daily productions as well as the utilisation of the blenders and associated filling areas. At the same time, employees in the warehouse know which containers are needed. This ensures that returnable containers in particular are prepared and made available to production in a timely manner.
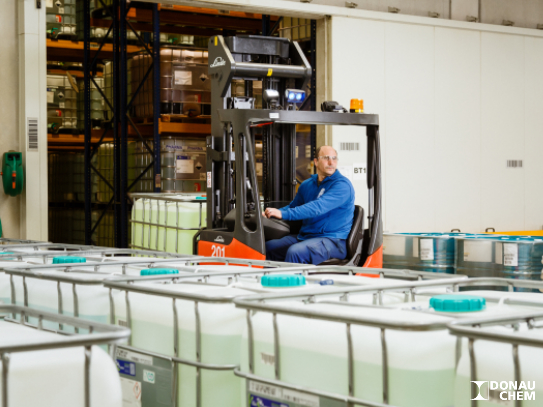
Filled IBC © Donauchem
Adherence to schedules through daily coordination and high commitment
The sequence of blending and filling as well as the allocation of the blending tanks are determined in daily production meetings. In close coordination with Mr. Zangana and Mr. Zehetner, the orders to be processed by noon the next day are defined here. Short-term orders are also discussed here and taken into account accordingly in the planning.
"Basically, we have a time span of three days to complete an order," explains Ing. Blaha. "For orders with several hundred small containers, filling naturally takes longer than for an IBC. Accordingly, we have to plan properly in advance. This is largely done by the planning department, but the orders are discussed every day with the help of the foremen."
In this way, it can be ensured that orders are completed on time and ready for pick-up at the agreed time. "On the one hand, we manage to do this through permanent coordination with the planning department, and on the other hand, I am lucky to have committed employees who act very independently and also work overtime if necessary," says Ing. Blaha.
Foreman as central hub in production
After scheduling, Mr. Zangana and Mr. Zehetner receive the order list and various work papers. The working papers list the pallets, containers, labels and any special requests from customers. Based on this list, they request all the necessary raw materials, give the order for preparing the containers and assign the employees for filling. "The production workers then prepare everything for filling, check the labels again and then fill the containers," explains Mr. Zangana.
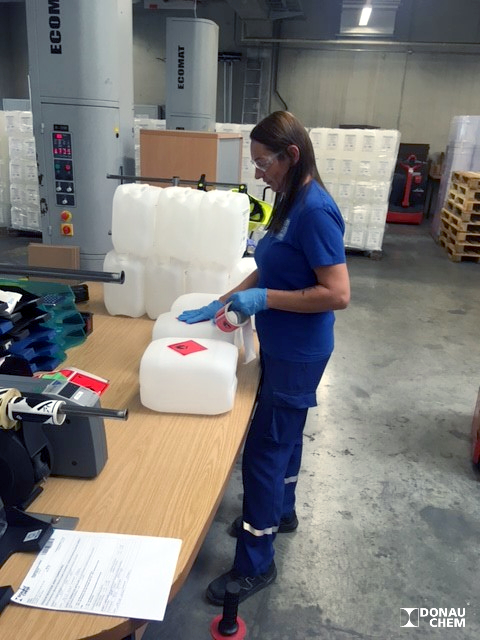
Ms Maritsch labelling canisters © Donauchem
The containers are labelled before or during filling. Before labelling, the fillers still have to check the containers. This is necessary because the container management system of Donauchem is partly based on loan and containers returned by the customer are not always completely cleaned.
In addition to checking the containers, all mixtures must undergo an assessment by the quality assurance department before they are filled. "Every mixture is analysed in the laboratory and only after approval do we fill it," says Roland Zehetner. "The finished filled mixture is then checked again before we deliver it to the customer."
Safety always comes first
In the production area, there are high requirements for the protection of the employees. "There is no point in completing an order very quickly if it causes an employee to suffer a chemical burn or there is an explosion," says Ing. Blaha. "Safety comes first, even if it has to be done quickly."
With solvents, the main focus is on the earthing of the containers and pumps. To avoid explosions, a uniform potential must prevail here. In the area of acids and alkalis, the main thing is to prevent etching with appropriate protective clothing. For dangerous acids such as hydrofluoric acid, employees must wear special suits, protective masks and rubber boots. In addition, entire areas are blocked off and prepared for certain mixtures and filling operations.
Wide range of filling options
A wide range of filling options are available at Donauchem - from large and small container systems to transfer systems and filling directly from mixing tanks or storage tanks. The container sizes include 1-litre, 5-litre and 20-litre canisters, drums and IBCs.
- Bulk container filling for up to 1000 litre IBCs
© Donauchem
- Filling barrels with up to 220 litres
© Donauchem
- It is also possible to fill directly from the mixing stand via direct hose filling
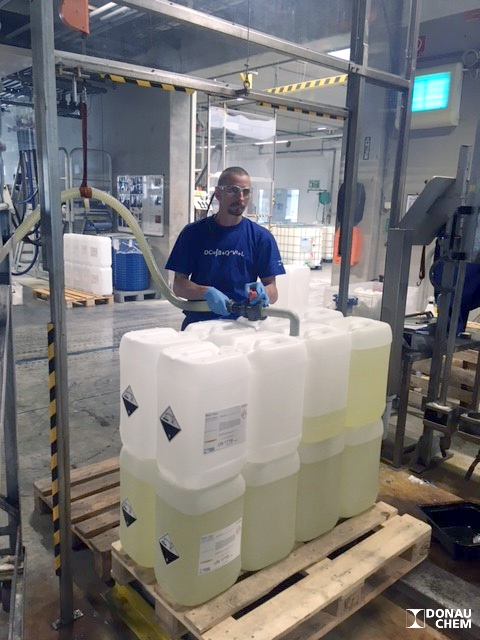
© Donauchem
- In decanting stations, we decant from IBCs or drums into small containers or produce small blends in IBCs - from 1 to 1,000 containers.
After cleaning and pallet finishing, it's off to the warehouse
Since Donauchem fills a large number of products and a wide variety of mixtures, the equipment and hoses have to be cleaned after each filling. Otherwise, product distortions could occur during subsequent fillings. "As soon as a filling is finished, the equipment and hose are emptied, washed and, depending on the water solubility of the filled product, either rinsed with the subsequent product or with water," explains Mr Zangana.
Not only the plant is cleaned after filling, but also each container. Apart from dust, this is mainly to remove splashes of chemicals that could possibly pose a risk to the customer. The containers are then placed on pallets (canisters and barrels) for pallet finishing, where they are wrapped in film and scanned.
The last step is the transfer to the warehouse. From there, it goes to the dispatch hall for truck packing or to the previously defined storage location for storage. "With us it doesn't happen that we have to look for a pallet," says Ing. Blaha, "when we enter a product, we immediately see in SAP where the pallet is."
Conclusion: Flexibility in production through high synergies
In the past, the different areas of Donauchem produced separately from each other: in one part of the industrial park in Pischelsdorf basic chemicals were mixed and filled, in another part consumer goods such as fertilisers or cleaners were produced. The solvents business was located on the outskirts of Vienna. By merging these areas in 2014, synergies have been created in Pischelsdorf that allow for faster and more flexible processing of customer orders. Committed and highly trained employees as well as close cooperation between the individual areas are the key factor for Donauchem's high flexibility.
www.donauchem.at