Plastic waste is a valuable raw material from which new recyclates can be produced again through recycling. With the EU Plastics Strategy, the requirements for the plastics industry to recycle plastics have increased enormously. Where Austria currently stands and which recycling processes are used, more on this in this blog.
With its extensive portfolio of industrial and special chemicals, Donauchem GmbH offers a whole range of products that are also used in the field of plastics recycling. In the raw material or tertiary recycling of plastic waste, work is very often carried out in aqueous media or in water cycles, where acids or alkalis are used to adjust the pH value.
In addition, various salt or electrolyte products are also used for buffering various water circuits and for water treatment. Subsequently, additives such as defoamers are used to prevent foam formation during various process steps, as well as other special chemicals for water softening.
In addition, we offer inorganic products from Donau Chemie Wassertechnik as precipitants, such as iron(III) chloride and polyaluminium chloride.
EU Plastics Strategy: The End of the Throwaway Society
The versatile applications of
plastics have increased the demand for plastics twentyfold in the last 50 years. With the consumption of plastics expected to double in the next 20 years, the
EU Plastics Strategy laid the foundation for a new plastics economy in early 2018.
Core elements of the strategy include:
- Recyclable design: by 2030, all plastic packaging placed on the EU market should be able to be reused or recycled in a cost-effective way.
- Better and more harmonised separate collection and sorting of plastic waste.
- Increase the recycled content in plastic products and strengthen the demand for plastic recyclate.
- Reduction of single-use plastics.
- Uniform rules for the identification and labelling of compostable and biodegradable plastics and the establishment of criteria for their use.
- Curbing microplastic pollution, including by restricting the use of microplastics in products and reducing the unintentional release of microplastics from tyres, textiles and paints.
- Innovate and invest in circular solutions, especially in the areas of separation (e.g. digital watermarking), recycling technologies as well as polymer design.
The amendment of the Waste Framework and Packaging Directive set higher rates for recycling and preparation for re-use of municipal waste (min. 50%) and plastic packaging waste (min. 55%) by 2030.
In addition, voluntary commitments by the plastics industry in the framework of the
Circular Plastics Alliance (CPA) are to ensure that ten million tonnes of recycled plastics are processed into new products for the EU market by 2025.
Need for action on plastics recycling in Austria
Austria is among the EU leaders in waste management and recycling. In the area of plastics recycling, however, there is still a need to catch up. In order to meet the ambitious EU targets, the plastics industry in Austria is primarily focusing on expanding the recyclability of its products and increasing the share of recycled materials.
The focus here is on plastic packaging. With a current recycling rate of 25%, the output quota must be increased from the current
75,000 t to 150,000 t by 2025 and to 165,000 t by 2030. Achieving these recycling targets requires the sufficient availability of high-quality input material. So far, however, the
low quantities of separated plastic still hinder the activities of plastics recyclers in large parts of Europe.
Starting points for measures to boost the circular economy were developed, among others, in the
10-point package of measures - Rethinking Plastics of the Austrian Chemical Industry Association (FCIÖ) as well as in the framework of a study on the
recyclability of packaging (FCIÖ).
An important basic document for the establishment and further development of the circular economy was created with the
Facts Matters study - Survey of the plastics material flow in Austria 2019. It provides a comprehensive material flow picture for plastics in Austria and covers the areas of production, processing and consumption, waste generation and recovery, plastic recyclates and areas of application.
According to the study, plastics processing companies in Austria used more than 160 kt of recycled plastics for the production of new products in 2019. This included recyclate from production and processing waste as well as recyclate from post-consumer waste.
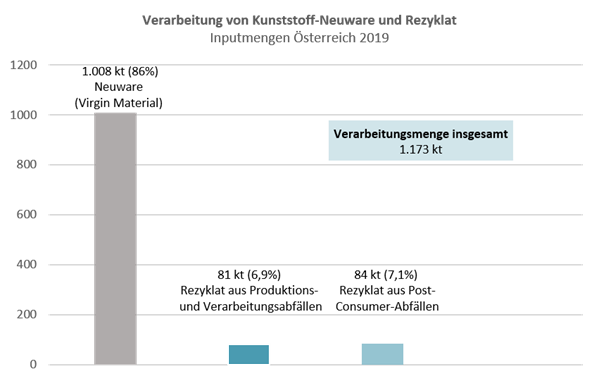
Source: Facts Matter results presentation Material flow diagram plastics in Austria 2019.
What types of recycling are there?
The terms recycling and recovery are often used synonymously. However, while recovery also includes the energetic use of plastic waste, recycling only refers to its material recovery. The following applies:
Recovery = recycling + energy recovery.
Plastics can basically be recovered in three different ways:
- Material recovery: The disposed plastics are mechanically processed. The chemical structure of the polymers is retained.
- Raw material recycling: The plastic polymers are broken down into their basic materials (monomers) by the action of heat or solvents and used again to produce new polymers or hydrocarbons.
- Energy recovery: The plastic waste is incinerated and used to generate electricity, steam or heat.
Another common type of classification is divided into four categories:
- Primary recovery: mechanical reprocessing into products with the same properties as the original product (closed-loop recycling).
- Secondary recovery: Mechanical reprocessing into products with worse properties than the original product (downgrading or downcycling).
- Tertiary recycling: Chemical recycling of the initial product by breaking down the polymer into its initial components (feedstock recycling). Biodegradable polymers also fall under this term.
- Quaternary recovery: Energetic recovery of the feedstock.
Primary and secondary recycling thus describe mechanical recycling, tertiary recycling raw material recycling and quaternary recycling energy recycling.
How high are the recycling rates of plastic waste in Austria?
A total of around 1 million tonnes of plastic waste is generated in Austria each year (2019: 0.98 million tonnes).
- "Pure" plastic waste accounts for about one sixth (2019: 17.5 %). This includes in particular plastic films, polyolefin waste and plastic packaging and containers.
- The majority is found in mixed waste such as bulky waste, end-of-life vehicles or waste electronic equipment, with varying degrees of plastic content (2019: 80.5 %).
- The remainder is accounted for by plastics in paints, varnishes, sludges and plasticisers (2019: 2 %).
Almost one third of plastic waste is attributable to plastic packaging (2018: 302 million t). Polyolefins again account for more than half of this.
The predominant form of treatment of plastic waste in Austria is energy recovery, followed by mechanical and feedstock recycling. The latter is only used to a very small extent.
In 2019, 86% of "unmixed" plastic waste was recycled, 13% incinerated and 1% landfilled. The majority of the waste containing plastics (around 90%) was thermally treated, 8% was recycled and only 2% was landfilled.
A total of 59 plants for sorting, processing and recycling plastic waste are available in Austria (2019):
- 15 sorting and processing plants for plastic waste or waste rich in plastics (annual capacity 273,300 t).
- 24 plants for mechanical recycling of plastic waste or waste rich in plastics (annual capacity approx. 416,000 t). In 19 plants, regranulates, flakes or regrind are produced; in five other plants, plastic products or semi-finished products are made from waste plastics.
- 19 plants for the processing/recycling of Styropor (annual capacity 3,400 t). The plants produce Styropor regrind, which is used e.g. in the building materials industry for the production of building materials.
- 1 pilot plant for chemical recycling using the re-oil process (annual capacity approx. 800 t). Basic materials for petrochemistry and fuel production are obtained from the plastic waste.
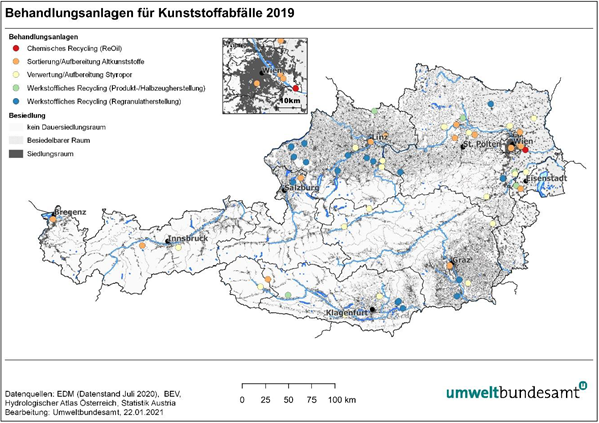
Source: BMK (2020) Status Report 2020
The right recycling process for every plastic
About 90% of plastics are made from just six different grades, which coincide with the main recycling classes. Hundreds more are used as special plastics in special applications. This enormous variety of different types of plastic ultimately also makes plastic recycling much more costly than is the case with glass or paper, for example.
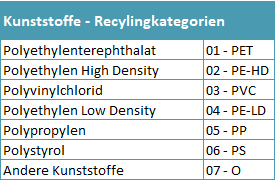
For mechanical recycling, it is essential that the waste materials are collected as cleanly and sorted as possible. Mixed waste is more difficult to recycle and involves a lot of effort in terms of logistics, sorting and cleaning.
Since feedstock recycling does not require a high degree of material purity, it is a good alternative to mechanical recycling. A functioning circular economy thus requires both - the technologies complement each other very well.
1. Mechanical recycling
Mechanical recycling is a combination of various mechanical pre-treatment steps and subsequent processing of the used plastic with the help of various processes. In principle, almost all types of plastics can be processed into recyclates by mechanical recycling. However, thermosets and elastomers can only be recycled to a limited extent due to their basic physical and chemical structure.
In addition to the different types of plastics, mechanical recycling is also confronted with the problem of limited recyclability. The stress caused by use and reprocessing leads to the degradation of the polymer chains and causes a reduction in quality. Polyethlyene, for example, shows lower strength, poorer processing properties and lower optical properties after several recycling cycles. Most plastics can therefore only be recycled about three to five times.
Example: Recycling process for post-consumer plastic packaging
The quality of the recyclate increases with the highest possible grade purity and low degree of contamination of the input material. The pre-treatment steps of sorting, shredding, separation, washing and cleaning play a central role in this respect.
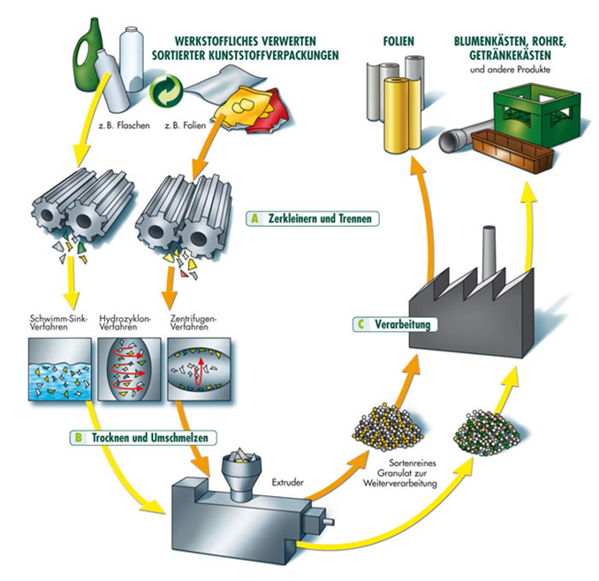
Recycling process for post-consumer plastic packaging (Graphic:
Ecoplast 2013)
1. Pre-sorting
The plastic waste is first sorted according to the different types of plastic and other materials such as metals using various methods (sieves, magnets, cameras, induction techniques, infrared scanning). Plastics consisting of only one plastic form single-variety fractions (PET, PS, PP, PE).
2. Shredding, cleaning and separation
The sorted used plastics are then shredded, washed and separated according to the density of the material. The floating-sink process, hydrocyclone process or centrifuge process in particular are used for this.
Cleaning is usually carried out with water. In order to remove stubborn household or industrial contaminants from the plastic chips, alkalis (usually
caustic soda) and cleaning enhancers (
surfactants and possibly other additives) are often used in addition. Disruptions to the separation process caused by surface foam or air bubbles adhering to the plastic can be remedied with
defoamers. Acids for neutralisation (e.g.
sulphuric acid),
defoamers,
flocculants and
activated carbon are used
to treat the waste water.
3. Drying and remelting
The dried plastic particles are then fed into the extruder where they are processed into granulate or recyclate at temperatures between 200 and 240 degrees Celsius. If further material components are added during melting, the granulate is called recompound or regenerate, while if it is melted down without any further additives, the granulate is called regranulate.
If there is no melting or remelting, the material is referred to as regrind. Thermoplastics can be remelted into pellets, while thermosets and elastomers are further used as ground material.
4. Further processing into plastic products
Subsequently, various plastics can be produced again from the recyclates. The sinter pressing, extrusion, injection moulding and intrusion processes are suitable for pure plastics. By modifying the processes, it is now possible to process mixed and contaminated plastic waste into products (downcycling).
2. Raw material recycling
In raw material or chemical recycling, the plastic polymers are broken down into their basic materials (monomers), which, depending on the recycling process, are used to produce new polymers or chemical substances such as liquid hydrocarbons, oil, petrol and gas. The process is particularly suitable for the treatment of mixed and contaminated waste streams that cannot be processed using mechanical recycling methods.
Various processes are available for the feedstock recycling of plastic waste, based on the mechanisms of polymer decomposition, hydrogenation of liquid hydrocarbons, thermal decomposition or gasification (solvolysis, pyrolysis, catalytic depolymerisation, hydrogenation, recycling in a blast furnace as a reducing agent, gasification process).
Compared to mechanical recycling, however, the raw material recycling processes are cost-intensive and significantly more complex in terms of equipment. Many of these processes are still years away from being suitable for industrial use. The highest level of development is currently in energy-intensive gasification processes, in which the plastics are strongly heated and then broken down by synthesis. In addition, large quantities of plastic waste are required for the economic operation of the process plants. Only in the case of recycling in the blast furnace are small batches possible.
The use of chemical recycling makes sense above all where the raw materials can be processed directly, i.e. in a refinery or petrochemical plant. One example is the
OMV ReOil plant at the Schwechat refinery, where waste plastic is used to produce synthetic crude oil from which high-quality plastics are made.
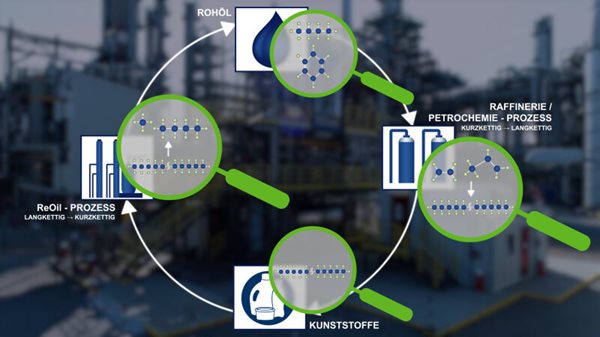
Pilot plant for chemical recycling at the Schwechat refinery in Austria. © OMV
Conclusion: The path to a circular plastics economy is complex
In order for a transformation towards a plastics circular economy to succeed, the value chains, material flows and product development processes must be changed. This means a deep intervention in the structures of the plastics industry. The development of recyclable plastic products, the availability of unmixed waste and the expansion of sorting and recycling capacities are currently among the greatest challenges facing the industry.
Details on our products for these applications can be found in our various product portfolios and
on request.
www.donauchem.at
Sources and related links:
Facts Matters – Erhebung des Kunststoffstoffstroms in Österreich 2019 - Status 16.August 2022
Studie Kunststoffabfälle in Österreich – Aufkommen und Behandlung, Umweltbundesamt 2017 - Status16.August 2022
Studie zum Thema „Vergleich der Eignung verschiedener Bewertungssysteme für die Recyclingfähigkeit von Verpackungsmaterialien in Österreich”, ofi/WKO 2021 - Status 16.August 2022
Technology Roademap - Sustainable Plastics Solution, Business Upper Austria – OÖ Wirtschaftsagentur GmbH 2021 - Status 16.August 2022
Plastics – The Facts 2020, Plastics Europe - Status 16.August 2022
Studie zur Umsetzung der Kunststoff Strategie in der Steiermark, 2020 - Status 16.August 2022
Recycling und Verwertung von Kunststoffabfällen – Probleme, Herausforderungen und Lösungen aus rohstofflicher und abfallwirtschaftlicher Sicht, DIin Andrea Eder, JKU Linz 2017 - Status 16.August 2022
10-Punkte Maßnahmenpaket „Rethinking Plastics “ so wird Österreich zur Vorzeigeregion für nachhaltige Kunststoffkreisläufe (FCIÖ) - Status 16.August 2022
Die Bestandsaufnahme der Abfallwirtschaft in Österreich - Statusbericht 2021 - Status 16.August 2022
Sortierung und Recycling von Kunststoffabfällen in Österreich, Status 2019 - Status 16.August 2022
Sortierung und Recycling von Kunststoffabfällen in Österreich, Kurzpräsentation Status 2019 - Status 16.August 2022
Circularity Report 2022, Plastics Europe - Status 16.August 2022
Circular Economy für Kunststoffe neu denken, VDI-Round Table 2021 - Status 16.August 2022
PlasticsEurope Austria - Status 16.August 2022
Projekt cleandanube - Status 16.August 2022
Recycling von Kunststoff: Abfall soll Öl für die Chemieproduktion liefern - Status 16.August 2022