Global supply chains have been under pressure since the second half of 2020 due to the disruption of the global shipping container system. However, while a few commodities were affected by extreme shortages after the first lockdown, the availability of all basic chemicals is now massively affected.
Low oil processing/refining (in refineries) causes broad commodity shortages
The fragile state of the global economy can be impressively seen in the development of the petroleum industry. Due to the economic collapse in the wake of the first global lockdown, there was more oil on the market than was needed. Oil tankers all over the world suddenly could no longer unload. Onshore storage facilities were filled to the top, as were pipelines, and there was no flow due to low demand for fuel. The global lockdown caused negative oil prices for the first time in history: Oil producers had to pay to be deprived of the commodity.
Today - one year later - physical demand for crude oil remains subdued due to the measures taken to contain the pandemic. Currently, it is still almost eight million barrels per day lower than before the pandemic. Accordingly, producing countries like Saudi Arabia, Russia and the USA have cut their production.
At the same time, demand from refineries has fallen worldwide. Due to the drastic drop in fuel consumption, production has been greatly reduced or put on maintenance since the beginning of the pandemic. As a further consequence, the production of petrochemical raw materials has been severely affected, which has now led to an extreme shortage of basic chemicals.
Many end products affected by raw material shortages
Basic chemicals based on crude oil and natural gas are used in 95 percent of all manufactured goods. Thus, the availability of basic raw materials stands and falls with crude oil production and refining: If less crude oil and natural gas is incorporated and further processed, then there is a shortage of the starting materials for a large number of other chemicals, which in turn are needed for intermediate and end products
In concrete terms, this means for the current situation that due to the relatively low refinery output, the supply chain is already disrupted at the very beginning. In the meantime, the raw material shortage extends all the way to the end product. For example, the lower ethylene and propylene production means that there is no ethylene and propylene oxide and all downstream products such as glycol and polyester are in short supply. Even corporations are sometimes on the verge of shutting down because they can no longer get production-relevant chemicals.
A look at the flow chart below illustrates the impact on end products if refineries continue to run at half load and the lockdowns continue for several months.
Petrochemicals: Flow/refinery process
Feedstock: Crude oil or natural gas/natural gas
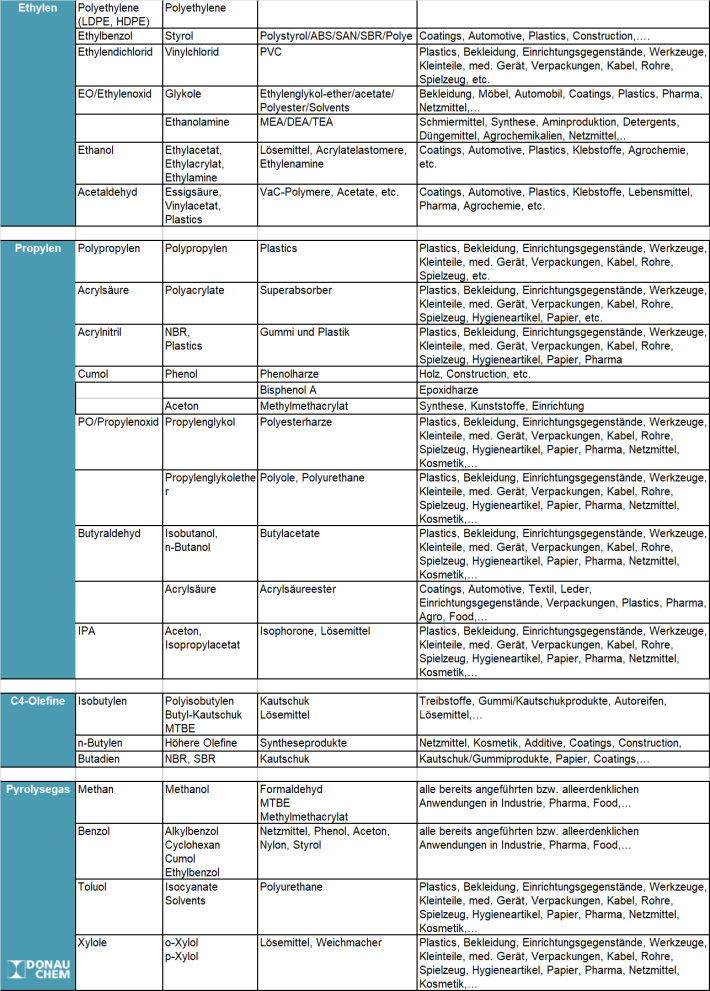
© Donauchem 2021
Mobility on the rise - oil production nevertheless remains low
The latest mobility data from Apple shows that mobility in Europe, the UK and the US has increased again since the beginning of 2021. This suggests that a broad recovery in overall fuel consumption is gaining momentum. However, OPEC+ recently announced that it would maintain its current production levels, although it had previously held out the prospect of introducing an additional 1.5 million barrels per day of production in April.
The background to this decision is lower demand estimates for the second quarter of 2021, justified by the impact that "continued lockdown measures, voluntary social distancing and other pandemic-related developments" have on economic activity. So, for the time being, lower production rates will remain, with a corresponding impact on base chemicals.
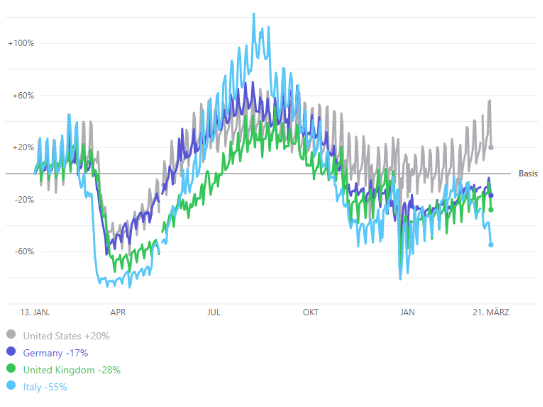
Apple confirms: Mobility on the rise - yet oil production remains low
(Source:
covid19.apple.com/mobility)
Force majeure exacerbates raw material shortages
A wave of force majeures (FMs) in Europe is putting unprecedented pressure on already tight chemical markets, with strong demand driving prices to record levels. In several product areas, materials are so scarce that downstream production is threatened by a shortage of raw materials. Some companies have had to declare FM due to lack of supply, which is highly unusual.
According to an analysis by ICIS, 43 products in Europe are currently affected by force majeures, in addition to existing global supply shortages caused by the US polar storm and plant closures in the Middle East and Asia. In particular, the disruption of key structural flows from the US to Europe due to the polar storm and weather effects in South Africa have affected supply in Europe for many import-dependent products. These include ethylene glycol, ethanolamines, methyl methacrylate (MMA), methyl acrylate, VAM, sulphuric acid and acetic acid.
Container shortage strains availability in Europe
The disruption to the global shipping container system began last year and continues into 2021 with a massive container shortage in Europe. Seven of the ten largest container ports in the world are located in China. As a result of this dependency, chemicals that rely on container transport from China to Europe are particularly affected by delays and skyrocketing costs:
1. Scarce shipping capacity:
Vessel capacities are currently at full capacity due to the huge boom in online trade. All available ships are at sea and are fully booked for weeks.
2. Lack of containers:
In the course of the first lockdown, containers were moved out to the hinterland worldwide. Many of these are still not in circulation.
3. Corona-related entry restrictions:
On the US West Coast, various import restrictions are causing container ships to be backed up and waiting times of up to two weeks. As a result, there is a shortage of containers in China for ships to Europe.
4. Delayed handling in ports:
Due to the corona situation in ports worldwide, the usual pace of work cannot be maintained, which means that the return of empty containers from the USA and Europe to Asia takes much longer than before.
5. Shift to Pacific routes:
Container shipping companies are shifting their shipments from Asia to the Western Pacific to meet the high demand from the USA. As a result, fewer ships are available between Asia and Europe.
6. Accident in the Suez Canal:
One of the world's largest container ships has broken down in the Suez Canal on 23 March, blocking the important transport link between Europe and Asia. The longer the blockage lasts, the more drastic the impact on the production and availability of goods in Europe will be.
In summary, this means container shortages on freight routes, container and goods congestion in destination ports and cargo ships that are fully booked for weeks. We do not expect this situation to ease before July 2021. In addition, the blockade of the Suez Canal could have an impact on global trade, as the Suez Canal considerably shortens the shipping routes between Europe and Asia.
Extreme price increases since November 2020
Commodity prices in Europe have risen 5-fold in many areas within the last few weeks due to shortages. This has now even gone so far that the raw materials are more expensive than the end product (e.g. surfactants). With regard to availability in Europe, the situation is exacerbated by the fact that goods produced in Europe are often exported because better prices for raw materials can currently be achieved in Asia and the USA - an absolute novelty that has never happened before!
At the same time, there has been a veritable explosion in freight prices since November, which peaked in mid-January with a three- to four-fold increase in prices. In the meantime, freight rates are slowly falling again. According to the Drewry World Container Index (WCI), however, the cost of a 40-foot container in traffic from Asia to Europe is still more than 300 per cent higher than in the previous year.
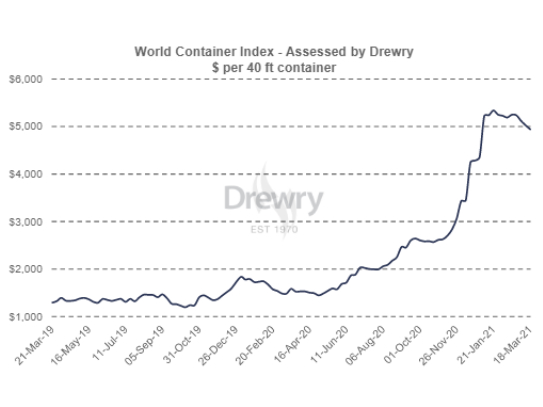
Quelle:
https://www.drewry.co.uk/supply-chain-advisors/supply-chain-expertise/world-container-index-assessed-by-drewry
Conclusion: Raw material shortages affect all basic chemicals
The investment focus on capacity in Asia at the expense of Europe and a heavy reliance on imports from Asia or the US has exposed Europe's vulnerability. Disrupted import flows from Asia and the US Gulf, combined with weak oil production and a chain of force majeures, is now affecting every stage of the value chain - right through to the final product. If the lockdowns continue in this form, a serious improvement in raw material availability is not to be expected.
www.donauchem.at
Related links/Downloads:
Whitepaper Shortage of raw material Q2/2021 (german)
Disturbed supply chains can be felt all the way to the furniture store (Der Standard, 20th July 2021)
Brake on growth in the construction industry - lack of raw materials (Industriemagazin, 4th August 2021)