In the current crisis, the need to flexibly outsource contract production is increasing. Many companies can no longer continue to operate as usual and are outsourcing their production due to Corona-related problems. British companies are also relocating production to the mainland to escape the consequences of Brexit.
Donauchem has a great deal of know-how in the area of contract production and is able to take over production in large quantities, even at very short notice. In this article, we would like to introduce you to two of our most experienced employees who will give you an insight into the heart of our contract production.
The employees behind Donauchem contract production
In our modern mixing plant in Lower Austria, Donauchem produces 20,000 tonnes of customised mixtures and solutions in liquid form per year for various industrial sectors - from small containers to tankers and tank wagons. The prerequisites for mixing and filling flammable and toxic substances in technical quality up to pharmaceutical and food quality are also met.
A total of 21 employees work in contract production, four of them in the mixing area. We asked Manuel Blaha and David Otzlberger about the technical changes that Corona made necessary, how contract production generally works and how short-term production is implemented.
Manuel Blaha has many years of experience as an employee and leads the team as production manager. David Otzlberger has been working at Donauchem for almost six years and, as a trained chemical process technician, has a lot of know-how in the mixing area.
Changes in the course of Corona and supply security
With Corona, a lot has changed abruptly - from one day to the next. "The production meetings are now held online, which took some getting used to" says Blaha. "Now the online meetings are going very well. There are definitely advantages associated with it, but for staff discussions or personal concerns, the interpersonal face-to-face is certainly still necessary."
As a further measure, production has been switched to two-shift operation since the beginning of the Corona crisis in order to maintain the ability to deliver. "This ensures that production can continue in the event of an employee falling ill and that the ability to deliver is maintained," says Blaha. For safety reasons, the two-shift operation still continues.
The demand for disinfectants has declined, but in contrast, contract production for the food and pharmaceutical industries has increased. In addition, production often has to be taken over in a flash, which is currently being outsourced by companies, mainly due to Corona and Brexit. Know-how and improvisation skills are in demand in such situations.
"The overall circumstances are unfamiliar at the moment, but the pressure itself is very manageable if you have a certain routine and experience," says Otzlberger. "In times of Corona we often have to improvise, so you have to know how to get out of the way. That takes a lot of pressure off."
High flexibility through daily meetings
The high flexibility and know-how of the staff in the mixing area make it possible to fulfil even short-term requests very promptly and according to the customer's requirements. "In daily production meetings we discuss how these orders can be taken into account and scheduled - be it by adapting mixing tank assignments or switching to containers, i.e. container blends," says Blaha.
Within a few days, productions in large and small quantities can be taken over in this way. "Recently we received a request for two barrels of cleaning agent that the customer urgently needed the following day," Otzberger recounts. "We mixed the required components in a container the next day and then delivered them straight away."
The incoming goods inspection of the raw materials used and the analysis of the mixtures are carried out in a laboratory of the quality assurance department of Donauchem, which was newly built especially for this purpose. Every delivery of raw materials is analysed here before it goes into production. Likewise, every mixture is checked before it is released and filled.
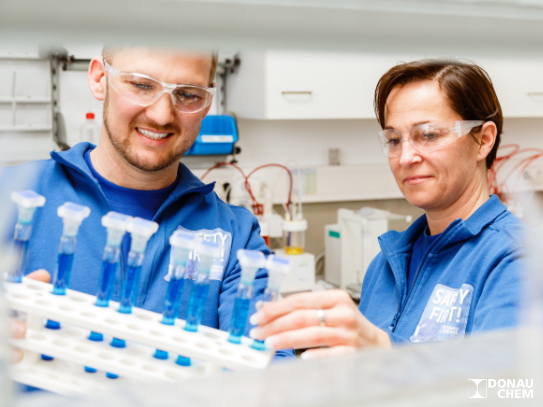
Picture shows analysis of a mixture in the laboratory © Pletterbauer 2021
Safety and competence are essential in the mixing sector
Safety is a top priority at Donauchem. The mixing area in particular harbours a number of risks. Although a high proportion of the mixtures are produced automatically, manual additions are often necessary. This requires not only appropriate protective clothing and exact compliance with work instructions, but above all a high level of competence on the part of the employees in the mixing area.
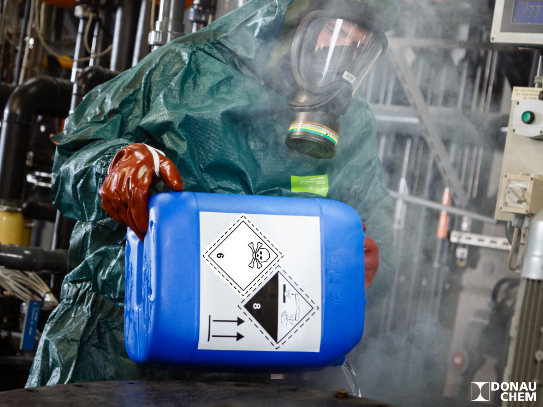
Picture shows Ing. Otzlberger adding hydrofluoric acid by hand - equipped with hydrofluoric acid suit, respiratory filter and ABEG rubber boots © Pletterbauer 2021
Mixers basically work according to recipes - only they don't make biscuits, they handle acids, alkalis and solvents that pose risks of chemical burns and explosions. "In general, it has to be said that being a mixer is a very demanding and responsible job," says Blaha. "For one thing, mixers often handle hazardous substances where there is always a residual risk - even though we are very concerned about safety. On the other hand, we deliver to the food and pharmaceutical industries, where the demands on the mixers are also very high."
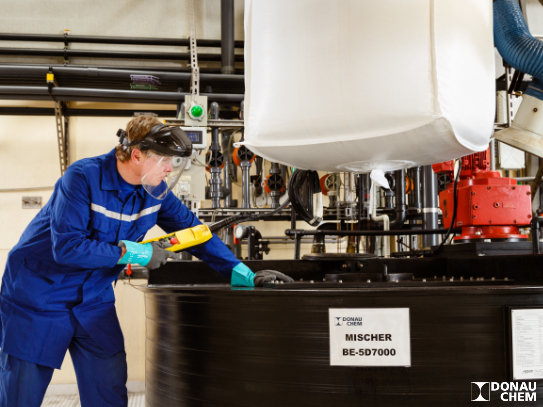
Picture shows food production with a suspended big bag at a mixing tank © Pletterbauer 2021
With regard to protective measures, only normal protective clothing and visors are necessary in food production. Here you can see that the raw material is added to the mixing tank from a 1,000 kg big bag.
Customised contract production according to customer requirements
Donauchem covers a very large product portfolio - from solvents, acids and alkalis in technical quality to pharmaceutical and food quality. In addition to private label productions, in-house products and "tailor made" developments are developed in cooperation with the research and development department, to ensure that customer requirements are met.
"In the company's own development laboratory, we realise new blends according to the specifications and wishes of our customers," says Blaha. "Often customers have certain ideas but don't know how to implement them. We then work out new blends according to customer requirements in cooperatoion with our blending department and quality assurance."
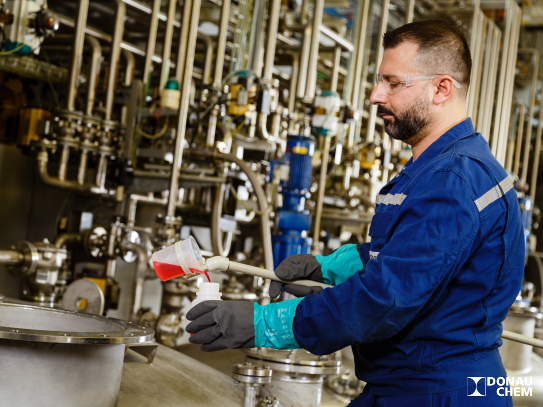
Taking samples from a mixing tank in the solvent area © Pletterbauer 2021
Short-term contract production using the example of disinfectants
In the course of the first lockdown, Donauchem received a flood of enquiries for the production of disinfectants. "It was an extremely difficult situation at the time, because Corona was on the rise but nobody knew how dangerous the virus was and how long this condition would last," says Blaha. "Solutions had to be found quickly: What do we have to do so that we can continue to produce. What happens if an employee in the mixing area becomes infected? How can we produce large quantities of disinfectant quickly?".
1. Exchange of raw materials
When demand for disinfectants boomed at the beginning of the pandemic, there was a massive shortage of raw materials in alcohols. Propyl alcohol, which is normally used for the production of disinfectants, was no longer available on the market. "We sought permission from the authorities for disinfectants according to WHO's recipe," explains Blaha. "Fortunately, the permit was granted very quickly and we were able to produce based on other raw materials."
2. Coping with extreme production volumes by being highly proactive
During the last year, the team produced several thousand litres of disinfectant. On a weekly basis, this amounted to around 100 tonnes, which were filled into containers, drums and canisters.
"When I look at the amount we produced last year, these are extreme numbers," says Otzlberger. "It's a labour challenge, of course, but during production you don't even consciously notice it, you just work through the orders as quickly as possible."
To cope with the high production volumes, weekend shifts and extended shifts were necessary. "The mixers and fillers worked very proactively and took responsibility. Despite this exceptional situation, every male and female employee made a tremendous contribution," Blaha tells us. "The mixers kept an eye on the availability of raw materials, the bottlers worked and labelled on weekends, and one employee managed four temporary workers. It was an outstanding performance by the entire production team."
The logistics, which were handled by the company's own and an external fleet of trucks, also proved challenging. "Logistics, warehouse and customer service all pulled together and really did a great job," says Blaha.
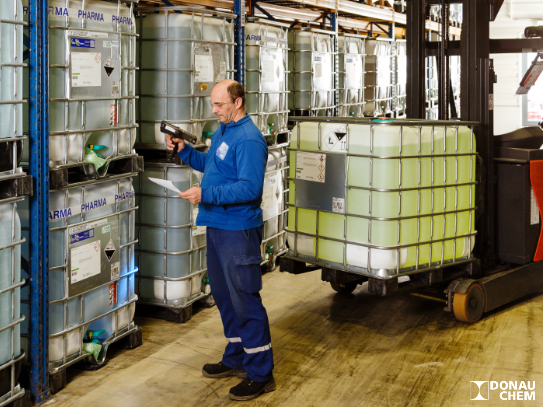
Scanning goods in the warehouse in preparation for delivery © Pletterbauer 2021
Conclusion: Those who rethink, become faster and better and will survive these times
Only companies that have sufficient resources to cope with the current changes will be fit for the future. Highly flexible contract production can be a key factor in meeting these challenges. Whether one's own capacities are exhausted, technological know-how is lacking in one's own company or tightened economic conditions make it difficult to manufacture in-house - the reasons for outsourcing production are manifold.
www.donauchem.at